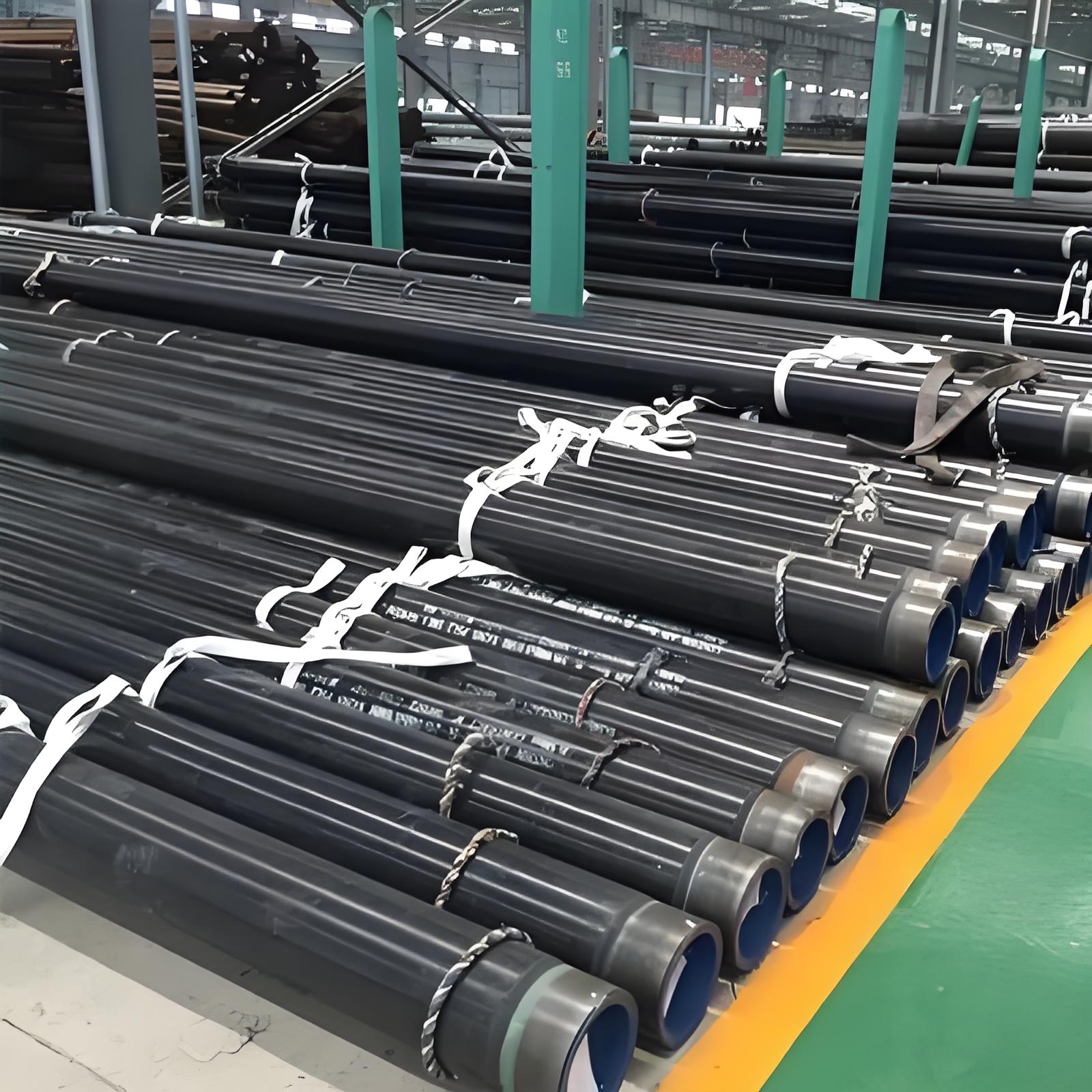
Technical Product Overview: 3PE Coated Steel Pipes for Oil and Gas Pipelines
Introduction
In the oil and gas industry, pipelines are critical for transporting crude oil, natural gas, and refined products over long distances, often in harsh environmental conditions. 3PE (Three-Layer Polyethylene) coated steel pipes have become a preferred choice for these applications due to their superior corrosion resistance, mechanical durability, and extended service life. This advanced coating system, consisting of a fusion-bonded epoxy (FBE) primer, a copolymer adhesive, and an outer polyethylene layer, provides robust protection against corrosion, abrasion, and physical damage, making it ideal for buried or submerged pipelines. This technical overview explores the material composition, mechanical and physical properties, coating specifications, manufacturing processes, and a comparative analysis of 3PE coated steel pipes against other coating systems. Our company specializes in producing high-quality 3PE coated steel pipes that meet international standards such as ISO 21809 and DIN 30670, ensuring reliability in demanding oil and gas applications. These pipes are designed to withstand extreme temperatures, chemical exposure, and mechanical stresses, offering a cost-effective solution that minimizes maintenance and extends pipeline lifespan to 30–50 years or more. The versatility of 3PE coating allows its application on various steel pipe types, including seamless, welded, and alloy steel pipes, making it suitable for diverse pipeline projects, from offshore oil transport to urban gas distribution. By providing detailed insights supported by technical tables, this article aims to demonstrate why 3PE coated steel pipes are an optimal choice for ensuring the integrity and efficiency of oil and gas pipelines.
1. Coating Composition and Properties
1.1 Coating Structure
The 3PE coating system is a multilayer anti-corrosion solution designed to protect steel pipes in oil and gas pipelines from environmental degradation. It consists of three functional layers, each contributing to the overall performance of the coating. The first layer is a fusion-bonded epoxy (FBE) primer, typically 100–200 µm thick, which provides excellent adhesion to the steel surface and acts as the primary corrosion barrier. This epoxy layer forms a strong chemical bond with the steel, offering resistance to moisture, chemicals, and cathodic disbondment. The second layer is a copolymer adhesive, approximately 170–400 µm thick, which serves as a bonding agent between the FBE primer and the outer polyethylene layer, ensuring a cohesive coating structure. The third layer is a high-density polyethylene (HDPE) or medium-density polyethylene (MDPE) topcoat, ranging from 1.6–4.7 mm in thickness, which provides mechanical protection against abrasion, impact, and physical damage during handling and installation. Table 1 details the typical specifications for each layer, as per standards like ISO 21809 and DIN 30670. The synergy of these layers results in a coating with high electrical resistance, low water absorption (less than 0.01%), and excellent stability across a wide temperature range (-40°C to 80°C). This makes 3PE coated steel pipes ideal for oil and gas pipelines exposed to corrosive soils, seawater, or chemical-rich environments, ensuring long-term durability and compliance with industry standards.[
Layer | Material | Thickness (µm) | Purpose |
---|---|---|---|
Layer 1 | Fusion-Bonded Epoxy (FBE) | 100–200 | Corrosion protection, adhesion to steel |
Layer 2 | Copolymer Adhesive | 170–400 | Bonding FBE and polyethylene layers |
Layer 3 | Polyethylene (HDPE/MDPE) | 1600–4700 | Mechanical protection, waterproofing |
Source: ISO 21809, DIN 30670
1.2 Mechanical Properties of Coating
The mechanical properties of the 3PE coating system are critical to its performance in protecting oil and gas pipelines from environmental and operational stresses. The FBE primer provides a strong adhesion strength of approximately 125 kg/cm² (per ASTM D4541), ensuring a firm bond with the steel surface that resists peeling and cathodic disbondment. The copolymer adhesive layer enhances the coating’s integrity by forming hydrogen or chemical bonds with the FBE and polyethylene layers, creating a seamless, durable structure. The outer polyethylene layer offers exceptional impact resistance, with tests showing it can withstand impacts without cracking, and abrasive resistance four times higher than bare steel. The coating’s flexibility allows it to elongate up to five times its original length without breaking, making it suitable for pipelines that require bending during installation. Table 2 summarizes key mechanical properties, highlighting the coating’s ability to endure harsh conditions. The 3PE coating maintains its integrity across a temperature range of -40°C to 80°C, ensuring performance in extreme environments like desert or Arctic regions. Its low water absorption and high electrical resistance prevent corrosion from moisture or stray currents, while its anti-aging properties ensure a service life of 30–50 years under normal operating conditions. These properties make 3PE coated steel pipes ideal for oil and gas pipelines, where reliability and longevity are paramount.[]
Property | Value | Test Standard |
---|---|---|
Adhesion Strength | 125 kg/cm² | ASTM D4541 |
Impact Resistance | No cracking under standard impact | ISO 21809 |
Abrasion Resistance | 4x bare steel | DIN 30670 |
Elongation | Up to 5x original length | ISO 21809 |
Water Absorption | < 0.01% | ISO 21809 |
Source: ISO 21809, DIN 30670, ASTM D4541
1.3 Physical Properties of Coating
The physical properties of the 3PE coating system enhance its suitability for oil and gas pipelines, particularly in buried or submerged environments. The FBE primer offers excellent chemical stability, resisting corrosion from acids, alkalis, and salts commonly found in soil or seawater. The polyethylene outer layer provides a high degree of electrical insulation, with a resistivity of approximately 10^16 Ω·cm, protecting pipelines from stray currents in electrically active environments. The coating’s thermal stability allows it to perform reliably at temperatures from -40°C to 80°C, with some formulations supporting up to 100°C for specific applications. Its low thermal conductivity reduces heat loss in pipelines carrying hot fluids, contributing to energy efficiency (heat loss is approximately 25% of bare steel pipes). The coating’s density, typically 0.93–0.96 g/cm³ for polyethylene, ensures a lightweight yet robust protective layer, reducing the overall weight of the pipeline by about one-eighth compared to traditional coatings. Table 3 outlines these properties, emphasizing their role in extending pipeline lifespan. The 3PE coating’s resistance to cathodic disbondment and low water absorption (less than 0.01%) prevent degradation in wet environments, making it ideal for offshore and onshore oil and gas pipelines. These physical properties, combined with rigorous manufacturing standards, ensure that 3PE coated steel pipes deliver long-term performance and reliability in challenging conditions.[]
Property | Value |
---|---|
Electrical Resistivity (Ω·cm) | 10^16 |
Thermal Stability (°C) | -40 to 80 (up to 100 for specific formulations) |
Water Absorption (%) | < 0.01 |
Density (g/cm³) | 0.93–0.96 (polyethylene layer) |
Thermal Conductivity | 25% of bare steel |
Source: ISO 21809, DIN 30670
2. Dimensional Specifications
2.1 Pipe Sizes and Coating Thickness
3PE coated steel pipes are available in a wide range of sizes to accommodate various oil and gas pipeline applications, from small-diameter urban gas lines to large-diameter offshore pipelines. According to standards like API 5L and ISO 21809, these pipes typically range from 2 inches to 56 inches (60.3 mm to 1422.4 mm) in outer diameter (OD), with wall thicknesses from SCH 10 to SCH 160 (2.11 mm to 50.01 mm). The 3PE coating thickness varies based on pipe diameter and application, with total coating thickness typically ranging from 2.0 mm for smaller pipes (<24” OD) to 3.3 mm for larger pipes (≥32” OD). Table 4 provides common dimensional specifications, including coating thicknesses for different pipe sizes. The coating process ensures uniform application across seamless, longitudinally welded (LSAW), spiral welded (SSAW), or electric resistance welded (ERW) pipes. Pipe ends can be plain, beveled, or threaded, with protective caps or rings applied to prevent damage during transport. The lightweight nature of the 3PE coating (approximately one-eighth the weight of steel) facilitates easier handling and installation, reducing project costs. These pipes are designed to meet the mechanical and environmental demands of oil and gas transport, ensuring leak-free performance and compliance with standards like API 5L, ASTM A53, and GB/T 9711. The flexibility of 3PE coating allows it to be applied to various pipe grades, including Gr. B, X42, X52, X60, X65, X70, and X80, ensuring versatility across pipeline projects.[
OD (Inches) | OD (mm) | Wall Thickness (mm) | Coating Thickness (mm) |
---|---|---|---|
2 | 60.3 | 3.91–7.82 | 2.0–2.5 |
4 | 114.3 | 6.02–13.49 | 2.0–2.7 |
8 | 219.1 | 8.18–22.23 | 2.5–3.0 |
16 | 406.4 | 9.53–30.96 | 2.5–3.0 |
24 | 609.6 | 9.53–38.10 | 2.7–3.0 |
32 | 812.8 | 12.70–50.01 | 3.0–3.3 |
56 | 1422.4 | 12.70–50.01 | 3.0–3.3 |
Source: API 5L, ISO 21809
2.2 Coating Application Standards
The application of 3PE coating on steel pipes for oil and gas pipelines adheres to strict standards to ensure consistency, durability, and performance. ISO 21809-1 and DIN 30670 outline the requirements for surface preparation, coating application, and quality testing. Surface preparation involves sandblasting to a near-white metal finish (SSPC-SP10 or ISO 8501-1 Sa 2½), removing rust, scale, and contaminants to ensure optimal adhesion of the FBE primer. The coating process begins with heating the pipe to 180–230°C, followed by electrostatic spraying of the FBE powder, which melts and bonds to the steel surface. The copolymer adhesive is then extruded onto the FBE layer, followed by the polyethylene topcoat, applied via side or upper extrusion to achieve uniform thickness. Table 5 details key application parameters. Post-coating tests, including holiday detection (to identify pinholes or defects), anti-peeling tests, impact strength tests, and indentation tests, ensure the coating meets performance standards. The coating’s thickness is measured at multiple points, with a minimum requirement and rejection threshold specified. These rigorous standards ensure that 3PE coated steel pipes can withstand the corrosive and mechanical challenges of oil and gas transport, providing reliable protection in diverse environments, from desert drylands to deep underwater regions. The process’s high degree of mechanization and stable parameters minimizes environmental impact and ensures consistent quality across large-scale pipeline projects.
Parameter | Specification |
---|---|
Surface Preparation | SSPC-SP10 / ISO 8501-1 Sa 2½ |
Heating Temperature (°C) | 180–230 |
FBE Thickness (µm) | 100–200 |
Adhesive Thickness (µm) | 170–400 |
Polyethylene Thickness (mm) | 1.6–4.7 |
Holiday Detection Voltage | Per ISO 21809 |
Source: ISO 21809, DIN 30670
3. Manufacturing Processes
3.1 Pipe Manufacturing
The manufacturing of 3PE coated steel pipes begins with the production of the base steel pipe, which can be seamless, longitudinally welded (LSAW), spiral welded (SSAW), or electric resistance welded (ERW), depending on the application and project requirements. Seamless pipes are produced by heating a steel billet to 1200–1300°C and extruding it into a hollow tube, followed by hot or cold rolling to achieve precise dimensions. Welded pipes are made from flat steel plates (skelp) formed into a cylindrical shape and welded using techniques like submerged arc welding (SAW) or electric resistance welding (ERW). The pipes are manufactured to standards like API 5L, ASTM A53, or GB/T 9711, with grades ranging from Gr. B to X80, ensuring compatibility with oil and gas transport. After forming, the pipes undergo surface preparation via sandblasting to achieve a clean, rough surface for optimal coating adhesion. The 3PE coating process involves heating the pipe, applying the FBE primer via electrostatic spraying, extruding the copolymer adhesive, and wrapping or extruding the polyethylene topcoat. Post-coating, the pipes are cooled using a water cooling system to 40–60°C to stabilize the coating. Rigorous quality control, including ultrasonic testing, hydrostatic testing, and coating inspections, ensures the pipes meet industry standards. This process results in durable, corrosion-resistant pipes suitable for the harsh conditions of oil and gas pipelines, ensuring long-term performance and minimal maintenance.
3.2 Coating Application Process
The application of the 3PE coating is a highly controlled process designed to ensure uniform coverage and long-term performance in oil and gas pipelines. The process begins with surface preparation, where the steel pipe is sandblasted to a near-white metal finish (SSPC-SP10 or ISO 8501-1 Sa 2½) to remove rust, scale, and contaminants. The pipe is then preheated to 40–60°C to remove moisture and enhance adhesion, followed by heating to 180–230°C for FBE application. The FBE powder is electrostatically sprayed onto the hot pipe, melting and bonding to form a corrosion-resistant primer layer. The copolymer adhesive is extruded onto the FBE layer, creating a strong bond with the subsequent polyethylene layer. The polyethylene topcoat, either HDPE or MDPE, is applied via side or upper extrusion, ensuring a uniform thickness of 1.6–4.7 mm. The coated pipe is rapidly cooled to 40–60°C using a water cooling system to stabilize the coating and prevent defects. A pipe-end grooving system may be used to remove coating from the ends, forming a groove (angle <30°) for easier welding during installation. Quality control includes holiday detection, adhesion tests, impact tests, and thickness measurements to ensure compliance with ISO 21809 and DIN 30670. This process, with its high degree of automation and stable parameters, ensures that 3PE coated steel pipes provide reliable corrosion protection and mechanical durability in oil and gas applications.
3.3 Quality Control and Testing
Quality control is integral to the production of 3PE coated steel pipes, ensuring they meet the rigorous demands of oil and gas pipelines. The base steel pipe undergoes mechanical testing, including tensile, yield, and elongation tests, to comply with standards like API 5L and ASTM A53. Coating quality is verified through a series of tests outlined in ISO 21809 and DIN 30670. Holiday detection uses a high-voltage leak detector to identify pinholes or defects in the coating, ensuring no weak points that could lead to corrosion. Adhesion tests, per ASTM D4541, measure the force required to peel the coating, with a minimum strength of 125 kg/cm². Impact strength tests assess the coating’s ability to withstand physical damage, while indentation tests evaluate resistance to penetration at various temperatures. Thermal analysis, conducted once per shift, verifies the coating’s stability. Coating thickness is measured at multiple points to ensure compliance with specified minimums (e.g., 2.0–3.3 mm total thickness). Additional tests, such as cathodic disbondment and water absorption, confirm the coating’s performance in corrosive environments. Pipes are also inspected for surface defects using ultrasonic or radiographic methods. These rigorous quality control measures ensure that 3PE coated steel pipes deliver consistent performance, extending pipeline lifespan to 30–50 years and reducing maintenance costs in oil and gas applications.[](https://www.continental-steel.com/blogs/Three-Layer-Polyethylene-3LPE-Coated-Line-Pipe.html)[](https://www.linkedin.com/pulse/coating-specifications-3pe-coated-pipe-continental-steel-co-ltd-uhocc)
4. Comparative Analysis with Other Coating Systems
To understand the advantages of 3PE coated steel pipes, a comparison with other coating systems used in oil and gas pipelines, such as fusion-bonded epoxy (FBE), 3PP (three-layer polypropylene), and galvanized coatings, is essential. Table 6 provides a detailed comparison. 3PE coating combines the corrosion resistance of FBE with the mechanical protection of polyethylene, offering superior performance compared to single-layer FBE, which lacks the robust physical protection of polyethylene and is less resistant to abrasion. 3PP coating, with a polypropylene topcoat, is suitable for higher temperatures (up to 110°C) but is more expensive and less flexible than 3PE, making it less ideal for bending pipelines. Galvanized coatings, while cost-effective, are prone to degradation in acidic or saline environments and have a shorter lifespan (5–15 years) compared to 3PE’s 30–50 years. 3PE’s low water absorption (<0.01%) and high electrical resistance make it ideal for buried or submerged pipelines, while its lightweight and flexible nature reduces installation costs. The coating’s compliance with ISO 21809 and DIN 30670 ensures it meets global standards for oil and gas pipelines, providing a cost-effective, durable solution compared to alternatives.[
Property/Coating | 3PE | FBE | 3PP | Galvanized |
---|---|---|---|---|
Corrosion Resistance | Excellent (FBE + PE) | Good (epoxy only) | Excellent (FBE + PP) | Moderate (zinc degrades) |
Mechanical Protection | Excellent (PE layer) | Moderate | Excellent (PP layer) | Poor |
Temperature Range (°C) | -40 to 80 | -40 to 100 | -40 to 110 | -29 to 425 |
Service Life (Years) | 30–50 | 15–30 | 30–50 | 5–15 |
Flexibility | High (PE elongates) | Low | Moderate | Low |
Cost (Relative) | Moderate | Low | High | Low |
Standards Compliance | ISO 21809, DIN 30670 | ISO 21809 | ISO 21809 | ASTM A53 |
Source: ISO 21809, DIN 30670, ASTM A53
5. Applications in Oil and Gas Pipelines
3PE coated steel pipes are widely used in oil and gas pipelines due to their robust corrosion resistance and mechanical durability. They are employed in long-distance transmission of crude oil, natural gas, and refined products, where pipelines are buried underground or submerged in seawater, facing corrosive soils, moisture, and chemical exposure. These pipes are also used in urban fuel gas distribution systems, ensuring safe and reliable delivery to residential and industrial consumers. In offshore applications, 3PE coated pipes withstand the harsh conditions of deep underwater environments, resisting corrosion from saltwater and physical damage from handling. They are suitable for pipelines transporting drinking water, as the coating prevents contamination and meets safety standards. The pipes’ ability to operate at temperatures from -40°C to 80°C makes them versatile for diverse environments, from Arctic regions to desert drylands. Specific applications include API 5L Gr. B to X80 pipelines for oil and gas transport, as well as storage tanks and groove piping systems. The 3PE coating’s flexibility and impact resistance allow for easy bending and installation, reducing costs in complex pipeline layouts. Its long service life (30–50 years) and low maintenance requirements make it a cost-effective solution for large-scale projects, ensuring reliable performance and environmental protection in oil and gas infrastructure.
6. Compliance with Industry Standards
3PE coated steel pipes are manufactured and tested to comply with international standards, ensuring their suitability for oil and gas pipelines. ISO 21809-1 specifies requirements for external coatings for buried or submerged pipelines, covering surface preparation, coating application, and performance testing. DIN 30670 outlines standards for polyethylene coatings, emphasizing thickness, adhesion, and durability. API 5L governs the base steel pipe, specifying grades like Gr. B, X42, X52, X60, X65, X70, and X80 for seamless and welded pipes. ASTM A53 covers black and hot-dipped zinc-coated pipes, ensuring compatibility with 3PE coating. The coating process includes rigorous testing, such as holiday detection, adhesion strength (ASTM D4541), impact resistance, and cathodic disbondment, to verify performance in corrosive environments. Certifications like ISO 9001 and third-party inspections (e.g., SGS, BV) ensure quality and compliance. The 3PE coating’s compliance with these standards guarantees its ability to protect pipelines from corrosion, abrasion, and mechanical damage, ensuring safety and reliability in oil and gas transport. Our company provides certified 3PE coated steel pipes, accompanied by material test reports (EN 10204 3.1), to meet the stringent requirements of global pipeline projects, ensuring long-term performance and regulatory adherence.[
7. Benefits of 3PE Coated Steel Pipes
The 3PE coating system offers numerous benefits for oil and gas pipelines, making it a preferred choice for protecting steel pipes in harsh environments. Its three-layer structure provides excellent corrosion resistance, with the FBE primer preventing chemical degradation and the polyethylene topcoat shielding against moisture and physical damage. The coating’s high adhesion strength (125 kg/cm²) ensures it remains bonded to the steel, even under stress or temperature fluctuations. Its flexibility and impact resistance allow for easy bending and handling, reducing installation costs by up to 20% compared to traditional coatings. The low water absorption (<0.01%) and high electrical resistance (10^16 Ω·cm) protect against corrosion from soil, seawater, or stray currents, extending pipeline lifespan to 30–50 years. The coating’s thermal insulation reduces heat loss to 25% of bare steel, saving energy in pipelines carrying hot fluids. Its lightweight nature (one-eighth the weight of steel) facilitates transport and installation, while its recyclability supports sustainable practices. The 3PE coating eliminates the need for secondary anti-corrosion equipment, reducing project costs and environmental impact. These benefits make 3PE coated steel pipes a cost-effective, reliable solution for oil and gas pipelines, ensuring safety, durability, and compliance with international standards.[](https://winsteelpipes.com/news/913.html)[](https://ridhimanalloys.home.blog/2020/02/11/3lpe-steel-pipe-coating-and-its-advantages-in-the-pipeline-industry/)
8. Recent Innovations and Trends
Recent advancements in coating technology have enhanced the performance of 3PE coated steel pipes for oil and gas pipelines. Innovations in FBE formulations have improved adhesion and corrosion resistance, with some primers now supporting low application temperature (LAT) processes for energy efficiency. Automated extrusion systems ensure precise application of adhesive and polyethylene layers, achieving consistent thickness and reducing defects. The integration of IoT sensors in pipeline monitoring allows real-time tracking of corrosion, pressure, and temperature, enabling predictive maintenance and extending service life. Advanced surface preparation techniques, such as laser cleaning, enhance coating adhesion by providing a cleaner surface than traditional sandblasting. The development of high-performance polyethylene blends has improved the coating’s resistance to abrasion and impact, particularly in offshore applications. Sustainability initiatives have led to eco-friendly coating processes, with reduced volatile organic compound (VOC) emissions and increased use of recyclable materials. These innovations align with the industry’s focus on efficiency, safety, and environmental responsibility. The adoption of 3PE coatings in smart pipeline systems, combined with compliance to standards like ISO 21809, ensures that these pipes meet the evolving demands of modern oil and gas infrastructure, providing enhanced durability and cost-effectiveness for both onshore and offshore projects.[
3PE coated steel pipes represent a state-of-the-art solution for oil and gas pipelines, offering unmatched corrosion resistance, mechanical durability, and cost-effectiveness. The three-layer system—comprising FBE primer, copolymer adhesive, and polyethylene topcoat—provides robust protection against environmental and chemical degradation, ensuring a service life of 30–50 years. Compliance with standards like ISO 21809, DIN 30670, and API 5L guarantees their suitability for demanding applications, from offshore oil transport to urban gas distribution. The coating’s flexibility, low water absorption, and high electrical resistance make it ideal for buried and submerged pipelines, while its lightweight design and ease of installation reduce project costs. Recent innovations, such as advanced FBE formulations, automated coating systems, and IoT integration, further enhance performance, aligning with industry trends toward sustainability and efficiency. Our company is committed to delivering high-quality 3PE coated steel pipes, manufactured and tested to the highest standards, to support the success of oil and gas pipeline projects worldwide. By choosing 3PE coated pipes, operators can achieve reliable, long-term performance, minimizing maintenance and ensuring environmental compliance. For more information or to request a quote, please contact us at [insert contact details]. With 3PE coated steel pipes, the future of oil and gas transport is secure, efficient, and sustainable.[]
You must be logged in to post a comment.