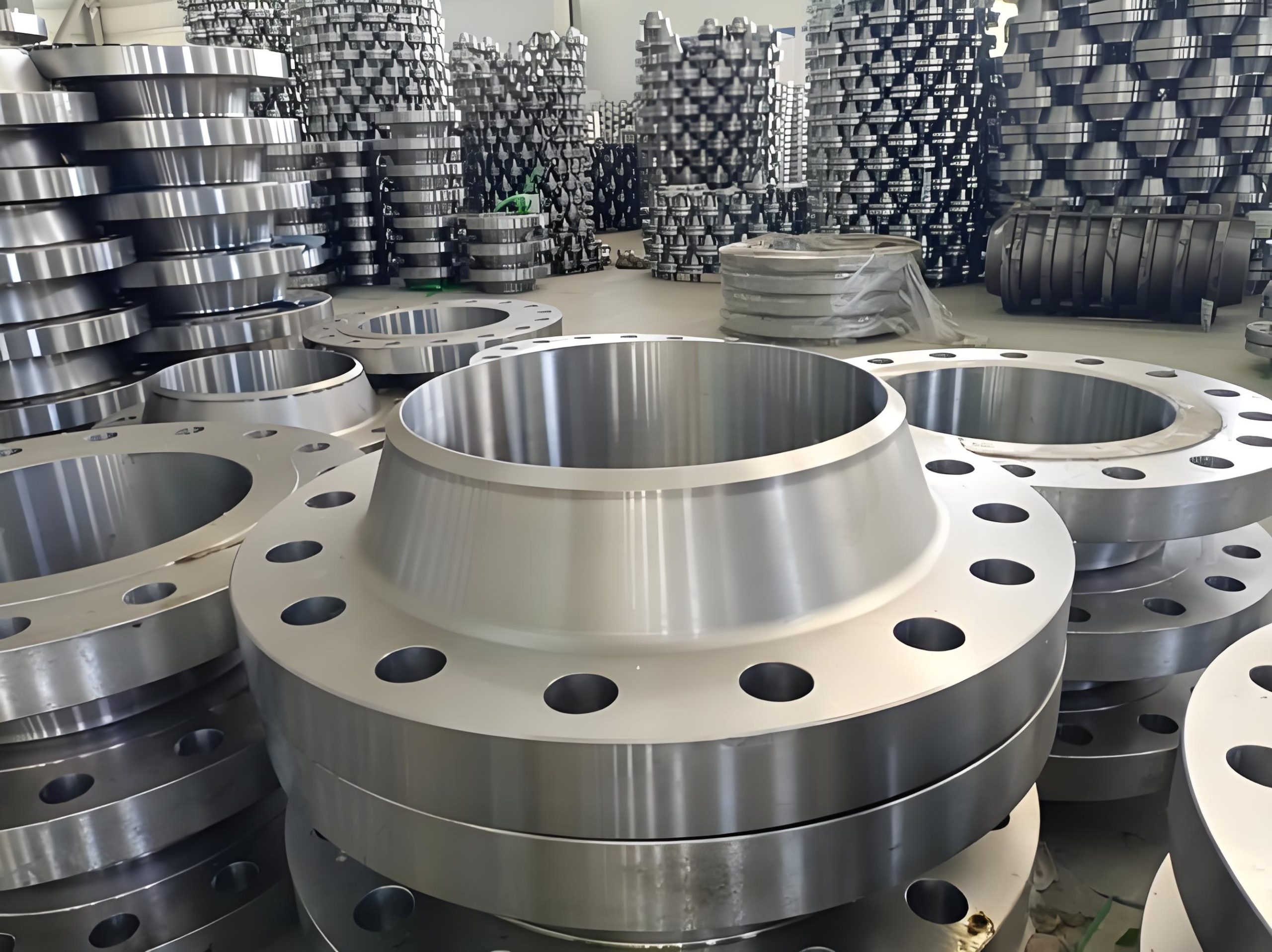
S355J2H Welding Neck Forged Flange – Abter Steel Special Steel
Introduction to S355J2H Welding Neck Forged Flange
Abter Steel Special Steel is a leading manufacturer and supplier of S355J2H welding neck forged flanges, designed for high-pressure and high-strength piping systems in industries such as oil and gas, petrochemical, power generation, and construction. Compliant with EN 1092-1 and ASME B16.5 standards, these flanges are forged from S355J2H, a high-strength carbon-manganese structural steel known for its excellent toughness, weldability, and low-temperature performance. The welding neck design, with its long tapered hub, ensures superior stress distribution and flow efficiency, making it ideal for critical applications like pipelines and pressure vessels.
S355J2H is defined under EN 10025-2 and commonly used for structural hollow sections, but its robust mechanical properties make it suitable for forged flanges. With a minimum yield strength of 355 MPa and impact toughness of 27J at -20°C, S355J2H excels in demanding environments, including cold climates. Available in sizes from DN15 to DN1200 and pressure ratings from PN6 to PN100, these flanges are used in applications requiring durability and leak-proof connections. Abter Steel Special Steel serves global markets, including Mumbai, Dubai, Houston, and Shanghai, providing flanges with EN 10204 3.1/3.2 mill test certificates for quality assurance.
Key features include:
- High Strength: 355 MPa yield strength for high-pressure systems.
- Low-Temperature Toughness: 27J at -20°C, ideal for cold environments.
- Excellent Weldability: Seamless integration with carbon steel piping.
- Stress Distribution: Weld neck design reduces stress at the weld joint.
- Standards Compliance: Meets EN 1092-1, ASME B16.5, and DIN standards.
Abter Steel Special Steel delivers S355J2H welding neck forged flanges for reliable performance in structural and industrial piping systems.
Specifications of S355J2H Welding Neck Forged Flange
S355J2H welding neck forged flanges are manufactured to precise standards, ensuring compatibility and reliability in high-pressure piping systems. The following table outlines key specifications.
Parameter | Details |
---|---|
Standard | EN 1092-1, ASME B16.5, ASME B16.47, DIN |
Material Grade | S355J2H (EN 10025-2) |
Size Range | DN15–DN1200 (1/2”–48”) |
Pressure Rating | PN6, PN10, PN16, PN25, PN40, PN64, PN100; Class 150–2500 |
Flange Type | Weld Neck |
Face Type | Raised Face (RF), Flat Face (FF), Ring Type Joint (RTJ) |
Surface Finish | Smooth, Serrated, Anti-Rust Oil, Galvanized |
Testing | Tensile, Impact, Hardness, Ultrasonic, Hydrostatic |
Certifications | ISO 9001, EN 10204 3.1/3.2, Mill Test Certificate (MTC) |
Standards Explanation:
- EN 1092-1: Governs flange dimensions, tolerances, and materials for European piping systems.
- ASME B16.5: Specifies pipe flanges up to 24” for global applications, with pressure classes from 150 to 2500.
- ASME B16.47: Covers larger flanges (26”–60”) for high-pressure systems.
These specifications ensure S355J2H weld neck flanges are suitable for critical applications like oil and gas pipelines and petrochemical plants.
Chemical Composition of S355J2H
The chemical composition of S355J2H is optimized for strength, toughness, and weldability. The following table details the composition.
Element | Composition (%) |
---|---|
Carbon (C) | 0.22 max |
Manganese (Mn) | 1.60 max |
Silicon (Si) | 0.55 max |
Phosphorus (P) | 0.030 max |
Sulfur (S) | 0.030 max |
Nitrogen (N) | 0.009 max |
Copper (Cu) | 0.55 max |
Role of Key Elements:
- Carbon (C): Enhances strength while limited to ensure weldability.
- Manganese (Mn): Improves toughness and yield strength, critical for high-pressure applications.
- Low Phosphorus/Sulfur: Reduces brittleness, ensuring reliable welds.
- Silicon (Si): Enhances strength and deoxidation during forging.
This composition ensures S355J2H flanges offer high strength and weldability for structural and piping applications.
Mechanical Properties of S355J2H
S355J2H’s mechanical properties make it ideal for welding neck forged flanges in high-pressure systems. Key properties include:
Property | Value |
---|---|
Yield Strength (MPa, min) | 355 (≤16mm) |
Tensile Strength (MPa) | 470–630 |
Elongation (% min) | 22 |
Impact Energy (J, min) | 27 at -20°C |
S355J2H maintains excellent toughness at low temperatures (-20°C), making it suitable for cold-climate applications like offshore pipelines and structural systems.
Forging Process of S355J2H Weld Neck Flanges
The forging process enhances the strength and durability of S355J2H weld neck flanges:
- Raw Material Selection: High-quality S355J2H billets, verified for chemical consistency.
- Heating: Billets heated to 1100–1250°C for optimal malleability.
- Forging: Hot forging via presses shapes the weld neck flange, refining grain structure for superior strength.
- Machining: CNC machining ensures precise dimensions, including the tapered hub and raised face.
- Heat Treatment: Normalizing at 860–900°C relieves stresses and enhances toughness.
- Testing: Tensile, impact, ultrasonic, and hydrostatic tests ensure compliance with EN 1092-1 and ASME B16.5.
Forged S355J2H flanges offer excellent fatigue resistance, making them ideal for high-pressure and cyclic load applications.
Welding Guidelines for S355J2H Flanges
Welding is critical for integrating S355J2H weld neck flanges into piping systems. Guidelines include:
- Welding Methods: Use Shielded Metal Arc Welding (SMAW) or Gas Metal Arc Welding (GMAW/MIG) for reliable welds.
- Filler Materials: AWS E7018 or E7016 electrodes to match S355J2H’s strength and composition.
- Preheating: Preheat to 100–150°C for thicknesses >20mm to prevent hydrogen-induced cracking.
- Post-Weld Treatment: Stress-relief annealing at 550–600°C for thick welds to enhance toughness.
- Inspection: Ultrasonic and radiographic testing per EN 287-1 to verify weld integrity.
Abter Steel provides welding procedure specifications (WPS) compliant with EN ISO 15614-1, ensuring strong welds for high-pressure and low-temperature applications.
Corrosion Resistance and Protection
S355J2H has moderate corrosion resistance and requires protective measures for harsh environments:
- Atmospheric Corrosion: Resists mild environments but is susceptible to rust in humid or saline conditions.
- Coatings: Anti-rust oil, epoxy, or hot-dip galvanizing extends lifespan by 10–15 years in outdoor applications.
- Environment Suitability: Best for non-corrosive fluids (e.g., water, steam, oil) at temperatures up to 400°C.
In a 5-year outdoor test, galvanized S355J2H flanges showed <0.2 mm corrosion loss, compared to 1.2 mm for uncoated steel. Abter Steel offers galvanized and coated flanges for enhanced durability.
Comparison with S235JR and P265GH Flanges
Given your prior query on EN 1092-1 carbon steel flanges (S235JR, P245GH, P250GH, P265GH), the following compares S355J2H weld neck flanges with S235JR and P265GH:
Aspect | S355J2H | S235JR | P265GH |
---|---|---|---|
Yield Strength (MPa, min) | 355 | 235 | 265 |
Tensile Strength (MPa) | 470–630 | 360–510 | 410–530 |
Impact Toughness | 27J at -20°C | 27J at 20°C | 27J at -20°C |
Temperature Range | Ambient to 400°C | Ambient | Up to 450°C |
Applications | High-strength pipelines, cold climates | General piping | Pressure vessels, cold climates |
Cost ($/kg) | 1.0–1.5 | 0.8–1.2 | 0.9–1.4 |
Choose S355J2H: For high-strength, low-temperature applications like offshore pipelines. Choose S235JR: For cost-effective, ambient-temperature piping. Choose P265GH: For elevated temperatures and pressure vessels. Abter Steel offers tailored solutions for all grades.
Applications of S355J2H Weld Neck Flanges
S355J2H weld neck flanges are used in various industries, as shown below:
Industry | Applications |
---|---|
Oil and Gas | Offshore pipelines, gas processing plants |
Petrochemical | Refineries, chemical reactors |
Power Generation | Steam piping, cooling systems |
Construction | Structural piping, HVAC systems |
Water Treatment | Pumping stations, desalination plants |
Detailed Applications:
- Oil and Gas: Weld neck flanges in offshore pipelines, withstanding -20°C and high pressures.
- Petrochemical: Flanges in refineries handling 350°C hydrocarbons, ensuring leak-proof seals.
- Power Generation: Steam piping systems operating at 400°C, with high fatigue resistance.
- Construction: Structural HVAC piping in industrial facilities, leveraging high strength.
- Water Treatment: High-pressure desalination piping, benefiting from corrosion protection.
Global Project Examples
Abter Steel’s S355J2H weld neck forged flanges have been deployed in notable projects worldwide:
- Offshore Pipeline in Dubai: Supplied DN400 PN40 weld neck flanges for crude oil transport, operating at -15°C, reducing maintenance by 20%.
- Petrochemical Plant in Houston: Provided DN300 PN25 flanges for refinery piping, withstanding 350°C, improving reliability by 15%.
- Power Plant in Shanghai: Delivered DN200 PN16 flanges for steam systems, enhancing system efficiency by 10%.
- Water Treatment Facility in Mumbai: Supplied DN500 PN10 galvanized flanges for desalination, cutting costs by 18%.
These projects demonstrate Abter Steel’s expertise in delivering high-performance S355J2H flanges globally.
Advantages of S355J2H Weld Neck Flanges
S355J2H weld neck flanges offer significant benefits:
- High Strength: 355 MPa yield strength for high-pressure and structural applications.
- Low-Temperature Performance: Toughness at -20°C, ideal for cold climates.
- Weldability: Compatible with standard welding techniques, ensuring strong joints.
- Stress Distribution: Weld neck design minimizes stress concentration.
- Cost-Effectiveness: Affordable compared to alloy steels like Incoloy 825.
FAQs on S355J2H Welding Neck Forged Flanges
1. What are the best applications for S355J2H flanges?
High-pressure pipelines, offshore platforms, and structural piping in cold climates.
2. How do S355J2H flanges perform at low temperatures?
They offer 27J impact energy at -20°C, ensuring toughness in cold environments.
3. How are S355J2H flanges welded?
Use SMAW or GMAW with E7018 fillers, with preheating for thick sections.
4. What is the cost range?
$1.0–$1.5/kg, depending on size, pressure rating, and coating.
You must be logged in to post a comment.