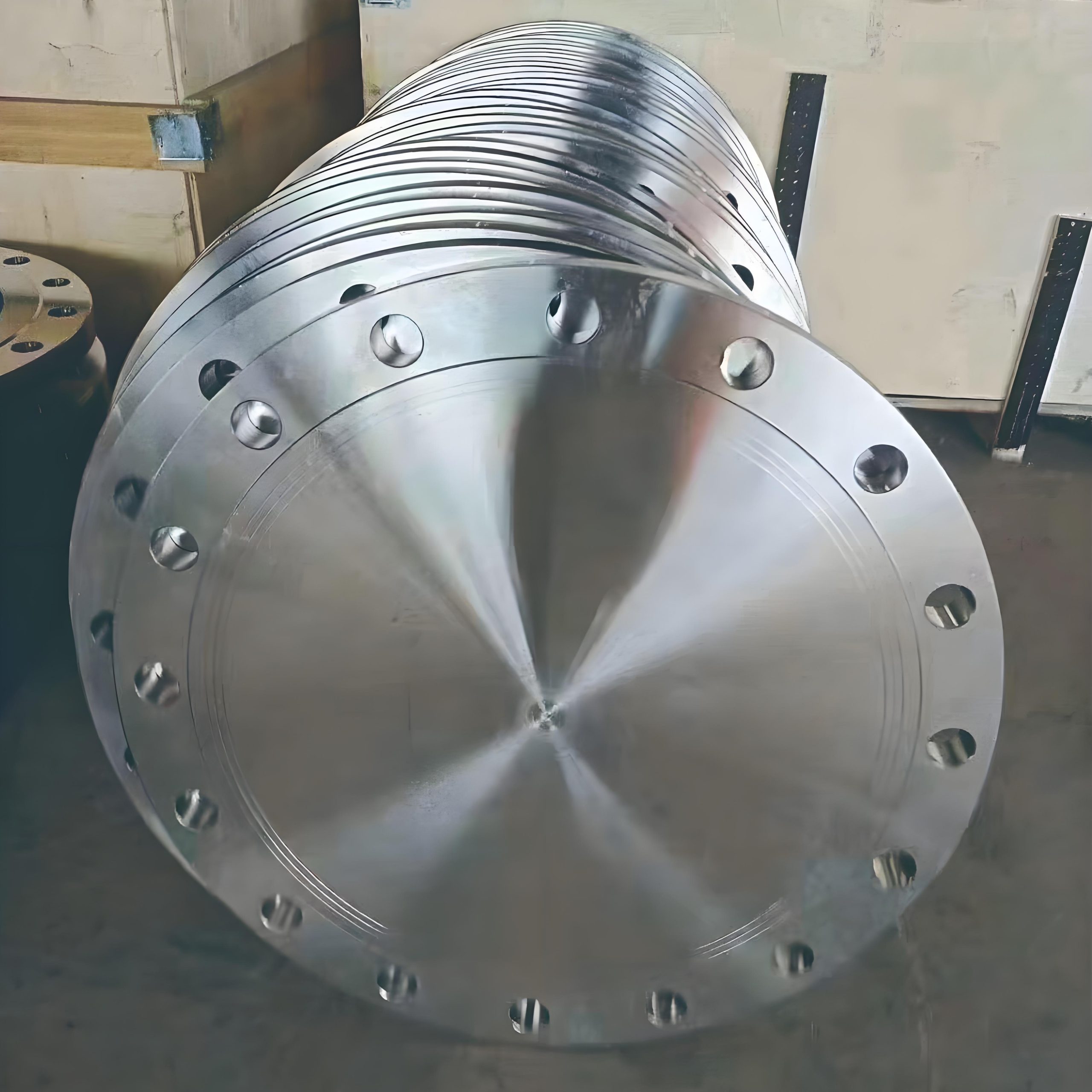
ASME SA336 Large Forgings Flange for Pipe System Cover
Overview of ASME SA336 Large Forgings Flange for Pipe System Cover
ASME SA336 is a standard specification for alloy steel forgings used in pressure and high-temperature applications, such as flanges, fittings, valves, and other components in piping systems. Large forgings flanges, compliant with ASME SA336, are critical for sealing pipe ends, vessel openings, or equipment inlets/outlets, functioning as pipe system covers. These flanges, often manufactured as blind flanges or channel cover flanges, provide robust, leak-proof closures for high-pressure, high-temperature environments in industries like petrochemical, power generation, and nuclear. Common grades include F22 Class 3 (2.25Cr-1Mo), F12, F6, and F91, which offer excellent creep resistance, corrosion resistance, and high-temperature strength. Large-diameter flanges, typically NPS 26” to 60”, comply with standards like ASME B16.47 Series A & B for dimensional and pressure ratings.
Key features include:
- High-Temperature Performance: Operates up to 816°C (1500°F), ideal for pressure vessels and boilers.
- Corrosion Resistance: Chrome-moly alloys resist oxidation and corrosion in acidic and high-temperature media.
- Forged Construction: Superior strength and durability compared to cast or machined flanges, critical for large-diameter applications.
- Versatile Applications: Used as blind flanges, channel covers, or custom forgings for pipe system closures.
ASME SA336 flanges are essential for ensuring the integrity of piping systems under extreme conditions, with grades like F22 CL3 and F91 preferred for their enhanced mechanical properties.
Specifications of ASME SA336 Large Forgings Flange
ASME SA336 large forgings flanges are manufactured to precise standards, ensuring reliability as pipe system covers. The following table outlines key specifications.
Parameter | Details |
---|---|
Standard | ASME SA336, ASME B16.47 Series A & B, ASME B16.5, ASTM A336 |
Material Grades | F1, F5, F6, F9, F11, F12, F22 (CL1, CL3), F91 |
Flange Type | Blind, Channel Cover, Weld Neck, Custom Forgings |
Size Range | NPS 26” to 60” (Series A & B); Custom sizes available |
Pressure Ratings | Class 75, 150, 300, 400, 600, 900, 1500, 2500 |
Facing | Raised Face (RF), Flat Face (FF), Ring Type Joint (RTJ) |
Manufacturing | Forged, Heat-Treated (Normalized, Quenched, Tempered) |
Testing | Hydrostatic, Ultrasonic, Tensile, Hardness, Impact, Notch Toughness |
Certifications | EN 10204 3.1/3.2, ISO 9001, ASME Section II, NACE MR0175 |
Heat Treatment | Normalized, Quenched and Tempered, per ASME SA336 |
Standards Explanation:
- ASME SA336: Covers alloy steel forgings for high-temperature and pressure applications, specifying chemical composition, mechanical properties, and heat treatment.
- ASME B16.47: Defines dimensions and tolerances for large-diameter flanges (NPS 26”–60”), Series A (MSS SP-44) and Series B (API 605).
- Testing Requirements: Includes hydrostatic testing (when specified), ultrasonic inspection, and notch toughness testing for critical applications.
Large forgings flanges are designed for high-pressure systems, with grades like F22 CL3 and F91 offering superior strength for pipe system covers in extreme conditions.
Applications of ASME SA336 Large Forgings Flange
ASME SA336 large forgings flanges are used as pipe system covers in industries requiring robust closures for high-pressure and high-temperature systems. The following table highlights key applications.
Industry | Applications |
---|---|
Petrochemical | Pressure vessel covers, reactor nozzles |
Power Generation | Boiler covers, turbine connections |
Nuclear | Reactor vessel closures, steam generator flanges |
Oil and Gas | Pipeline terminations, offshore platform covers |
Chemical Processing | Acid reactors, high-pressure vessel covers |
Detailed Applications:
- Petrochemical: F22 CL3 and F91 flanges are used as pressure vessel covers and reactor nozzles, resisting corrosion from hydrocarbons and high temperatures.
- Power Generation: Boiler covers and turbine connections rely on F12 and F91 flanges for their creep resistance and ability to withstand steam at 816°C.
- Nuclear: Reactor vessel closures and steam generator flanges use F22 CL3 for their notch toughness and high-pressure performance, critical for safety.
- Oil and Gas: Pipeline terminations and offshore platform covers benefit from F6 and F91’s corrosion resistance in sour gas environments.
- Chemical Processing: Acid reactors and high-pressure vessel covers use F22 and F12 flanges for their resistance to acidic and alkaline media.
The forged construction and alloy composition of SA336 flanges ensure durability and reliability as pipe system covers in extreme environments.
Chemical Composition of ASME SA336 Grades
The chemical composition of SA336 alloy steel grades is tailored for high-temperature strength and corrosion resistance. The following table details the composition for key grades used in large forgings flanges.
Element | F22 CL3 (%) | F12 (%) | F6 (%) | F91 (%) |
---|---|---|---|---|
Carbon (C) | 0.05–0.15 | 0.05–0.15 | 0.15 max | 0.08–0.12 |
Manganese (Mn) | 0.30–0.60 | 0.30–0.80 | 0.50–1.00 | 0.30–0.60 |
Phosphorus (P) | 0.040 max | 0.045 max | 0.040 max | 0.020 max |
Sulfur (S) | 0.040 max | 0.045 max | 0.030 max | 0.010 max |
Silicon (Si) | 0.50 max | 0.10–0.60 | 1.00 max | 0.20–0.50 |
Chromium (Cr) | 1.90–2.60 | 0.80–1.25 | 11.5–13.5 | 8.0–9.5 |
Molybdenum (Mo) | 0.87–1.13 | 0.44–0.65 | 0.50 max | 0.85–1.05 |
Nickel (Ni) | – | – | 1.00 max | 0.40 max |
Vanadium (V) | – | – | – | 0.18–0.25 |
Role of Key Elements:
- Chromium: Enhances corrosion and oxidation resistance at high temperatures.
- Molybdenum: Improves creep resistance and strength in elevated-temperature environments.
- Vanadium (F91): Increases strength and toughness, critical for high-pressure applications.
- Low Phosphorus and Sulfur: Minimize embrittlement, ensuring toughness.
The composition ensures SA336 flanges are robust for high-pressure pipe system covers.
Physical Properties of ASME SA336 Grades
The physical properties of SA336 alloy steels support their use in large forgings flanges. The following table summarizes properties for F22 CL3, a common grade.
Property | Value |
---|---|
Density | 7.85 g/cm³ (0.283 lb/in³) |
Melting Range | 2600–2700°F (1427–1482°C) |
Thermal Conductivity | 35.9 W/m·K at 100°C (24.7 BTU/ft·h·°F) |
Specific Heat Capacity | 470 J/kg·K at 20°C (0.112 BTU/lb·°F) |
Coefficient of Thermal Expansion | 13.1 µm/m·°C at 20–1000°C (7.3 µin/in·°F) |
Modulus of Elasticity | 200 GPa (29 × 10⁶ psi) at 20°C |
The moderate thermal expansion and high melting range ensure dimensional stability in high-temperature pipe system covers.
Mechanical Properties of ASME SA336 Grades
The mechanical properties of SA336 grades ensure reliability in large forgings flanges. The following table summarizes properties for key grades in the heat-treated condition.
Property | F22 CL3 | F12 | F6 | F91 |
---|---|---|---|---|
Tensile Strength (MPa) | 515–690 | 415–585 | 515–690 | 585–760 |
Yield Strength (MPa) | 310 min | 220 min | 310 min | 415 min |
Elongation (%) | 18 min | 20 min | 20 min | 20 min |
Hardness (HB) | ~235 max | ~197 max | ~235 max | ~248 max |
Temperature-Dependent Properties (F22 CL3, Approximate):
Temperature | Tensile Strength (MPa) | Yield Strength (MPa) | Elongation (%) |
---|---|---|---|
20°C (68°F) | 515 | 310 | 18 |
600°C (1112°F) | 400 | 200 | 22 |
F91 and F22 CL3 offer superior strength for high-pressure pipe system covers, while F12 is cost-effective for less demanding applications.
Fabrication of ASME SA336 Large Forgings Flange
SA336 large forgings flanges are manufactured through open-die or closed-die forging, using processes like hammering, pressing, or rolling to shape tube blanks or ingots. The forged construction eliminates defects like segregation or porosity, ensuring high strength. Flanges are typically normalized, quenched, and tempered to achieve required properties. Welding for installation uses:
- Shielded Metal Arc Welding (SMAW): Common for field welding.
- Gas Tungsten Arc Welding (GTAW/TIG): High-precision welds for critical applications.
Use matching filler metals (e.g., AWS E9018-B3 for F22) and preheat to 200–250°C to prevent cracking. Post-weld heat treatment (PWHT) at 1250°F (677°C) minimum is required to relieve stresses.
Heat Treatment
SA336 flanges undergo specific heat treatments to achieve desired properties:
- F22 CL3: Quenched at 1650–1700°F (899–927°C) and tempered at 1250°F (677°C) minimum for high strength.
- F12: Normalized at 1650–1700°F (899–927°C) and tempered for ductility.
- F6: Annealed or normalized and tempered for corrosion resistance.
- F91: Normalized at 1900–1975°F (1040–1080°C) and tempered at 1350–1470°F (730–800°C) for creep resistance.
Heat treatment ensures optimal performance in high-temperature pipe system covers.
ASME SA336 Large Forgings Flange FAQs
1. What is the purpose of SA336 large forgings flanges as pipe system covers?
They seal pipe ends, vessel openings, or equipment inlets, ensuring leak-proof closures in high-pressure, high-temperature systems.
2. Why choose F22 CL3 or F91 over F12?
F22 CL3 and F91 offer higher strength and creep resistance, ideal for extreme conditions, while F12 is cost-effective for moderate applications.
3. What standards govern large-diameter flanges?
ASME B16.47 Series A & B for NPS 26”–60”, and ASME B16.5 for smaller sizes, ensure dimensional and pressure rating compliance.
4. What testing is required for SA336 flanges?
Hydrostatic, ultrasonic, tensile, hardness, impact, and notch toughness tests ensure compliance with ASME SA336 and A961/A961M.
5. How do SA336 flanges compare to SA105 carbon steel flanges?
SA336 alloy steel flanges offer superior high-temperature strength and corrosion resistance compared to SA105, which is better for ambient conditions.
Conclusion
ASME SA336 large forgings flanges, made from alloy steels like F22 CL3, F12, F6, and F91, are critical for sealing pipe systems as covers in high-pressure, high-temperature applications. Compliant with ASME SA336, ASME B16.47, and A961/A961M, these flanges offer exceptional creep resistance, corrosion resistance, and strength. Their forged construction ensures durability in petrochemical, power generation, and nuclear industries.
You must be logged in to post a comment.