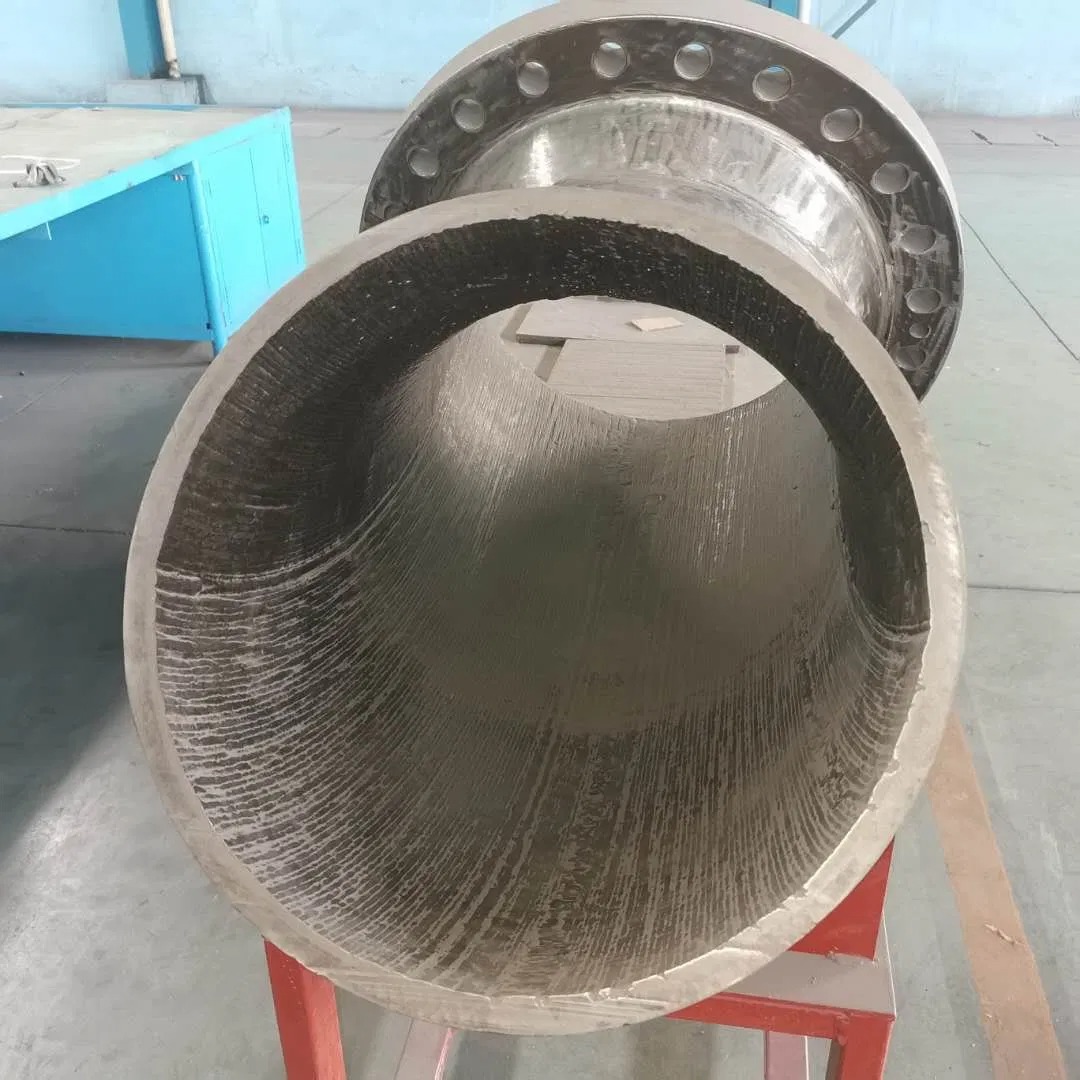
Abstract
High chromium alloy lined pipes and bimetal lined pipes with high chrome alloy are advanced engineering solutions designed to address the challenges of wear, corrosion, and high-temperature environments in demanding industrial applications. These pipes combine the mechanical strength of a base material, typically carbon or low-alloy steel, with the exceptional abrasion and corrosion resistance of high chromium alloys. This article provides an in-depth exploration of these products, detailing their physical properties, chemical composition, manufacturing processes, technological advancements, quality requirements, and comparative performance data. Through rigorous analysis and tabular comparisons, we aim to highlight the superior qualities of these pipes and their critical role in industries such as mining, power generation, cement production, and petrochemical processing.
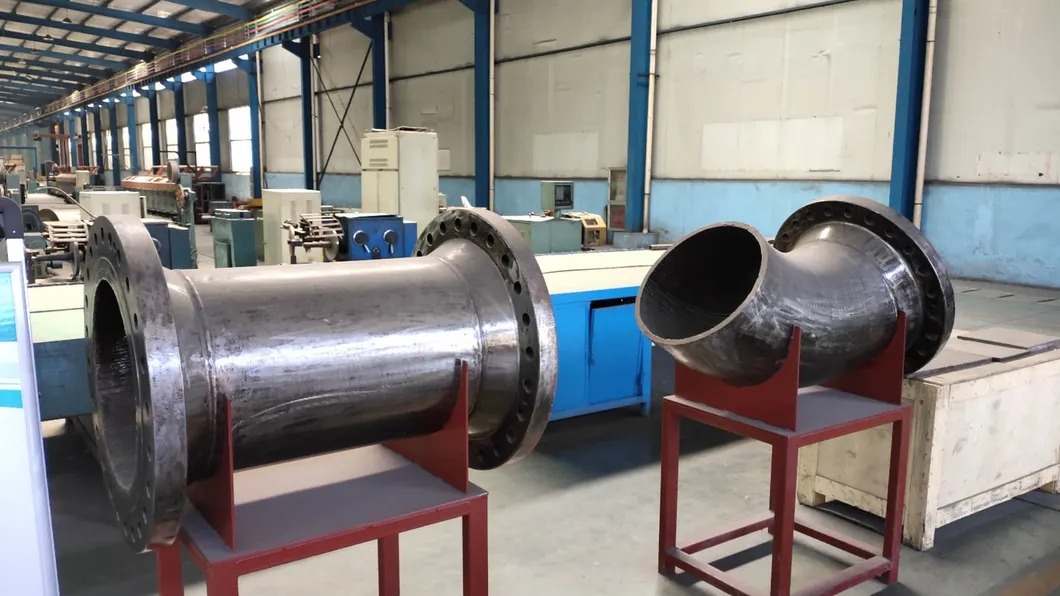
1. Introduction
In industries where pipelines are subjected to abrasive materials, corrosive fluids, or extreme temperatures, conventional steel pipes often fail to deliver long-term reliability. High chromium alloy lined pipes and bimetal lined pipes with high chrome alloy have emerged as robust solutions to these challenges. These pipes are engineered to combine the structural integrity of a steel outer layer with the wear and corrosion resistance of a high chromium alloy inner lining. The bimetallic construction leverages the strengths of both materials, resulting in a product that offers extended service life, reduced maintenance costs, and enhanced operational efficiency.
This article aims to provide a comprehensive introduction to high chromium alloy lined pipes and bimetal lined pipes, focusing on their material properties, manufacturing processes, and performance characteristics. We will also compare these pipes with other abrasion-resistant materials, such as low-alloy and high-alloy cast iron, to underscore their advantages. The discussion is supported by detailed tables, data comparisons, and insights into quality control and technological advancements.
2. Overview of High Chromium Alloy Lined Pipes and Bimetal Lined Pipes
2.1 High Chromium Alloy Lined Pipes
High chromium alloy lined pipes are typically composed of a seamless steel outer pipe, often made of Q235 carbon steel or low-alloy steel, with an inner lining of high chromium cast iron or alloy. The high chromium alloy, such as KmTBCr28 or Cr20, contains a significant percentage of chromium (typically 12–28%) and other alloying elements like molybdenum, nickel, and carbon. These elements form hard carbides (e.g., M7C3) within the microstructure, which contribute to exceptional wear resistance and corrosion resistance.
2.2 Bimetal Lined Pipes with High Chrome Alloy
Bimetal lined pipes consist of two distinct metallic layers bonded through advanced manufacturing processes, such as centrifugal casting or vacuum suction casting. The outer layer is typically carbon steel or low-alloy steel, providing mechanical strength and impact resistance, while the inner layer is a high chromium alloy designed to withstand abrasion, corrosion, and high temperatures. The bimetallic structure ensures a metallurgical bond between the layers, enhancing durability and reliability under harsh operating conditions.
2.3 Applications
These pipes are widely used in industries such as:
-
Mining: For conveying abrasive slurries, tailings, and concentrates.
-
Power Generation: For transporting coal ash, pulverized coal, and desulfurization slurries.
-
Cement Production: For handling abrasive raw materials and clinker.
-
Petrochemical Industry: For processing corrosive fluids and gases.
-
Metallurgy: For conveying molten metals and slag.
3. Physical Properties
The physical properties of high chromium alloy lined pipes and bimetal lined pipes are critical to their performance in demanding environments. These properties include hardness, toughness, thermal conductivity, and resistance to thermal shock.
3.1 Hardness
High chromium alloys, such as KmTBCr28, exhibit a Vickers hardness of 1500–1800 HV (equivalent to 55–62 HRC), attributed to the presence of M7C3 carbides. This hardness is significantly higher than that of low-alloy steels or standard cast iron, making these pipes ideal for abrasive environments. The outer steel layer typically has a hardness of 150–200 HB, providing sufficient toughness to withstand mechanical impacts.
3.2 Toughness and Impact Resistance
The bimetallic structure enhances toughness by combining the ductile outer steel layer with the hard inner alloy. The outer layer absorbs mechanical shocks, while the inner layer resists wear. This combination results in excellent impact resistance, with bimetal pipes capable of withstanding dynamic loads in applications like slurry transport.
3.3 Thermal Conductivity and Shock Resistance
High chromium alloys have moderate thermal conductivity, which, combined with the steel outer layer, ensures efficient heat dissipation. The bimetallic construction also provides resistance to thermal shock, allowing the pipes to operate in environments with rapid temperature changes, such as power plant boilers or petrochemical reactors.
3.4 Density and Weight
The density of high chromium cast iron is approximately 7.7–7.9 g/cm³, slightly higher than that of carbon steel (7.85 g/cm³). However, the bimetallic design optimizes weight by using a thinner high chromium alloy lining, reducing the overall weight compared to solid alloy pipes.
Table 1: Physical Properties Comparison
Material/Property
|
High Chromium Alloy (KmTBCr28)
|
Low-Alloy Cast Iron
|
Carbon Steel (Q235)
|
Stainless Steel (316L)
|
---|---|---|---|---|
Hardness (HV/HRC)
|
1500–1800 (55–62 HRC)
|
400–500 (40–50 HRC)
|
150–200 HB
|
200–250 HV
|
Density (g/cm³)
|
7.7–7.9
|
7.2–7.4
|
7.85
|
8.0
|
Thermal Conductivity (W/m·K)
|
15–20
|
40–50
|
50–60
|
16
|
Impact Toughness (J/cm²)
|
5–10 (inner layer)
|
10–15
|
50–70
|
100–150
|
Thermal Shock Resistance
|
High
|
Moderate
|
Moderate
|
High
|
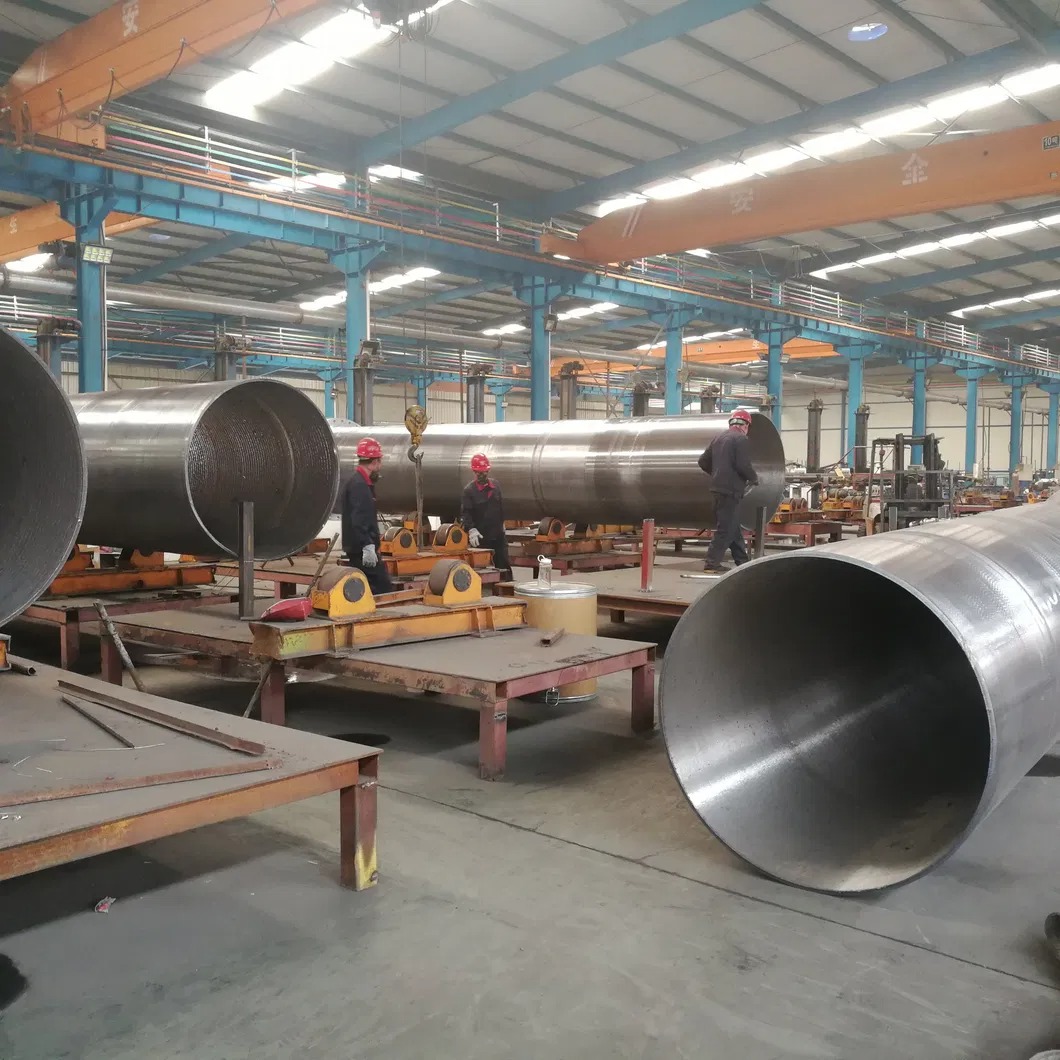
4. Chemical Composition
The chemical composition of the high chromium alloy lining is a key determinant of its performance. The alloy typically contains a high percentage of chromium, along with carbon, molybdenum, nickel, and other elements to enhance specific properties.
4.1 Typical Composition
-
Chromium (Cr): 12–28%. Chromium forms hard carbides (M7C3) and enhances corrosion resistance.
-
Carbon (C): 2.0–3.5%. Carbon contributes to the formation of carbides, increasing hardness and wear resistance.
-
Molybdenum (Mo): 0.5–3.0%. Improves high-temperature strength and corrosion resistance.
-
Nickel (Ni): 0.5–2.0%. Enhances toughness and resistance to low-pH corrosion.
-
Manganese (Mn): 0.5–1.5%. Improves hardenability and toughness.
-
Silicon (Si): 0.5–1.5%. Enhances fluidity during casting and improves oxidation resistance.
-
Rare Earth Elements (Re): Trace amounts. Improve microstructure and wear resistance.
4.2 Comparison with Other Materials
Low-alloy cast iron typically contains lower chromium content (1–5%) and lacks the complex carbide structure of high chromium alloys. Stainless steel (e.g., 316L) has a higher nickel content but lower hardness, making it less suitable for abrasive environments.
Table 2: Chemical Composition Comparison
Element (%)
|
High Chromium Alloy (KmTBCr28)
|
Low-Alloy Cast Iron
|
Carbon Steel (Q235)
|
Stainless Steel (316L)
|
---|---|---|---|---|
Chromium (Cr)
|
26–28
|
1–5
|
0.05–0.2
|
16–18
|
Carbon (C)
|
2.0–3.5
|
2.5–3.5
|
0.12–0.2
|
0.03 max
|
Molybdenum (Mo)
|
0.5–3.0
|
0–0.5
|
–
|
2–3
|
Nickel (Ni)
|
0.5–2.0
|
0–1.0
|
–
|
10–14
|
Manganese (Mn)
|
0.5–1.5
|
0.5–1.0
|
0.3–0.7
|
2.0 max
|
Silicon (Si)
|
0.5–1.5
|
1.0–2.0
|
0.3 max
|
1.0 max
|
5. Process Requirements
The manufacturing of high chromium alloy lined pipes and bimetal lined pipes involves sophisticated processes to ensure a strong metallurgical bond, uniform lining thickness, and high-quality surface finish.
5.1 Centrifugal Casting
Centrifugal casting is the primary method for producing straight bimetal pipes. In this process:
-
A seamless steel pipe (outer layer) is placed in a rotating mold.
-
Molten high chromium alloy is poured into the mold, where centrifugal forces distribute the alloy evenly along the inner surface.
-
The alloy solidifies under high gravity (up to 70 times that of conventional casting), ensuring a dense, defect-free lining.
-
The resulting pipe is heat-treated to optimize the microstructure and relieve residual stresses.
5.2 Vacuum Suction Casting
For complex shapes, such as elbows and tees, vacuum suction casting is used. This process involves:
-
Creating a foam mold of the desired shape.
-
Placing the mold inside a steel outer pipe.
-
Pouring molten high chromium alloy under vacuum conditions to fill the mold and bond with the steel.
-
Removing the foam mold, leaving a precise alloy lining.
5.3 Heat Treatment
Post-casting heat treatment is critical to enhance the properties of the high chromium alloy. The process typically includes:
-
Normalizing: Heating to 1050°C and air cooling to refine the microstructure.
-
Tempering: Heating to 760°C to reduce brittleness and improve toughness.
5.4 Surface Finishing
The inner lining is machined or polished to achieve a smooth surface, reducing friction and preventing material buildup. The outer steel surface may be coated with anti-corrosion layers for additional protection.
6. Technology Advancements
Recent advancements in manufacturing technology have significantly improved the performance and cost-effectiveness of high chromium alloy lined pipes and bimetal lined pipes.
6.1 Lost Foam Casting
The lost foam casting process has revolutionized the production of complex bimetal components, such as elbows and reducers. This method allows for precise control over the alloy lining thickness and ensures a seamless metallurgical bond, reducing the risk of delamination.
6.2 Advanced Bonding Techniques
Techniques such as explosive welding and roll bonding have been adapted for bimetal pipe production. These methods create a stronger interlayer bond, enhancing the pipe’s ability to withstand thermal and mechanical stresses.
6.3 Alloy Development
The incorporation of rare earth elements (e.g., cerium, lanthanum) into high chromium alloys has improved their microstructure, increasing wear resistance and toughness. For example, ZG40CrMnMoNiSiRe, a rare earth alloy steel, offers superior performance in high-temperature abrasive environments.
6.4 Automation and Quality Control
Automated casting and inspection systems, including ultrasonic testing and X-ray analysis, ensure consistent quality and detect defects in real time. These technologies have reduced production costs and improved reliability.
7. Quality Requirements
To meet the stringent demands of industrial applications, high chromium alloy lined pipes and bimetal lined pipes must adhere to rigorous quality standards.
7.1 Material Quality
-
The high chromium alloy must have a uniform microstructure with no cracks, porosity, or inclusions.
-
The steel outer layer must meet standards such as API 5L or ASTM A106 for mechanical strength and weldability.
7.2 Bonding Integrity
-
The metallurgical bond between the alloy lining and steel outer layer must withstand shear stresses exceeding the strength of the base metal.
-
Non-destructive testing (NDT) methods, such as ultrasonic and dye penetrant testing, are used to verify bond integrity.
7.3 Dimensional Accuracy
-
The inner lining thickness must be uniform, typically ranging from 2–5 mm, to ensure consistent wear resistance.
-
The pipe’s outer diameter, wall thickness, and length must comply with specifications such as ASME B36.10 or DIN standards.
7.4 Performance Testing
-
Wear Resistance: Tested using ASTM G65 (dry sand/rubber wheel test), with high chromium alloys achieving wear rates 20 times lower than carbon steel.
-
Corrosion Resistance: Evaluated in acidic (pH < 4) and high-temperature environments, with KmTBCr28 showing minimal degradation.
-
Pressure Rating: Pipes must withstand pressures up to 35 MPa, depending on the application.
7.5 Certifications
Pipes must comply with international standards, such as:
-
API 5LD for bimetal clad pipes.
-
ASTM A335 for chrome-moly alloy pipes.
-
ISO 9001 for quality management systems.
8. Comparative Analysis
To highlight the advantages of high chromium alloy lined pipes and bimetal lined pipes, we compare their performance with other abrasion-resistant materials, including low-alloy cast iron, high-alloy cast iron, and ceramic-lined pipes.
Table 3: Performance Comparison
Property/Material
|
High Chromium Alloy Lined Pipe
|
Low-Alloy Cast Iron
|
High-Alloy Cast Iron
|
Ceramic-Lined Pipe
|
---|---|---|---|---|
Wear Resistance (ASTM G65, mm³ loss)
|
0.5–1.0
|
5–10
|
1.5–3.0
|
0.1–0.5
|
Corrosion Resistance (pH < 4)
|
Excellent
|
Poor
|
Good
|
Excellent
|
Impact Resistance
|
High
|
Moderate
|
Low
|
Poor
|
Thermal Shock Resistance
|
High
|
Moderate
|
Moderate
|
Poor
|
Cost (USD/m, 6-inch pipe)
|
200–300
|
100–150
|
150–200
|
300–400
|
Service Life (years, abrasive slurry)
|
5–10
|
1–3
|
3–5
|
7–12
|
8.1 Wear Resistance
High chromium alloy lined pipes outperform low-alloy cast iron and high-alloy cast iron in wear resistance due to their high carbide content. Ceramic-lined pipes offer slightly better wear resistance but are brittle and prone to cracking under impact.
8.2 Corrosion Resistance
The high chromium content ensures excellent corrosion resistance in low-pH and high-temperature environments, comparable to ceramic-lined pipes and superior to low-alloy cast iron.
8.3 Impact and Thermal Shock Resistance
The bimetallic structure provides superior impact and thermal shock resistance compared to ceramic-lined pipes, which are susceptible to cracking. High-alloy cast iron has moderate performance but lacks the toughness of bimetal pipes.
8.4 Cost-Effectiveness
While high chromium alloy lined pipes are more expensive than low-alloy cast iron, their extended service life and reduced maintenance costs make them more cost-effective in the long term. Ceramic-lined pipes, although highly durable, are significantly more expensive.
9. Case Studies
9.1 Mining Industry
A copper mine in Chile replaced low-alloy cast iron pipes with high chromium alloy lined pipes for slurry transport. The new pipes reduced downtime by 60% and extended service life from 2 years to 7 years, resulting in annual savings of $500,000.
9.2 Power Generation
A coal-fired power plant in China installed bimetal lined pipes for ash conveying. The pipes withstood abrasive coal ash and high temperatures (up to 600°C), reducing maintenance costs by 40% compared to stainless steel pipes.
9.3 Cement Production
A cement plant in India adopted high chromium alloy lined elbows for clinker transport. The elbows exhibited a wear rate 5 times lower than high-alloy cast iron, extending replacement intervals from 1 year to 4 years.
10. Future Trends
10.1 Material Innovations
Ongoing research focuses on developing high chromium alloys with enhanced toughness and corrosion resistance through the addition of rare earth elements and nano-carbides. These advancements could further extend service life and reduce costs.
10.2 Smart Manufacturing
The integration of Industry 4.0 technologies, such as real-time monitoring and predictive maintenance, is expected to optimize the production and performance of bimetal pipes.
10.3 Sustainability
Manufacturers are exploring eco-friendly casting processes and recyclable materials to reduce the environmental impact of bimetal pipe production.
11. Conclusion
High chromium alloy lined pipes and bimetal lined pipes with high chrome alloy represent a pinnacle of engineering innovation, combining the strength of steel with the wear and corrosion resistance of high chromium alloys. Their superior physical properties, optimized chemical composition, and advanced manufacturing processes make them indispensable in industries facing abrasive and corrosive challenges. Through detailed comparisons and case studies, this article has demonstrated their advantages over alternative materials, such as low-alloy and high-alloy cast iron and ceramic-lined pipes. As technology continues to evolve, these pipes are poised to deliver even greater performance, cost-effectiveness, and sustainability, solidifying their position as a critical component in modern industrial systems.
You must be logged in to post a comment.