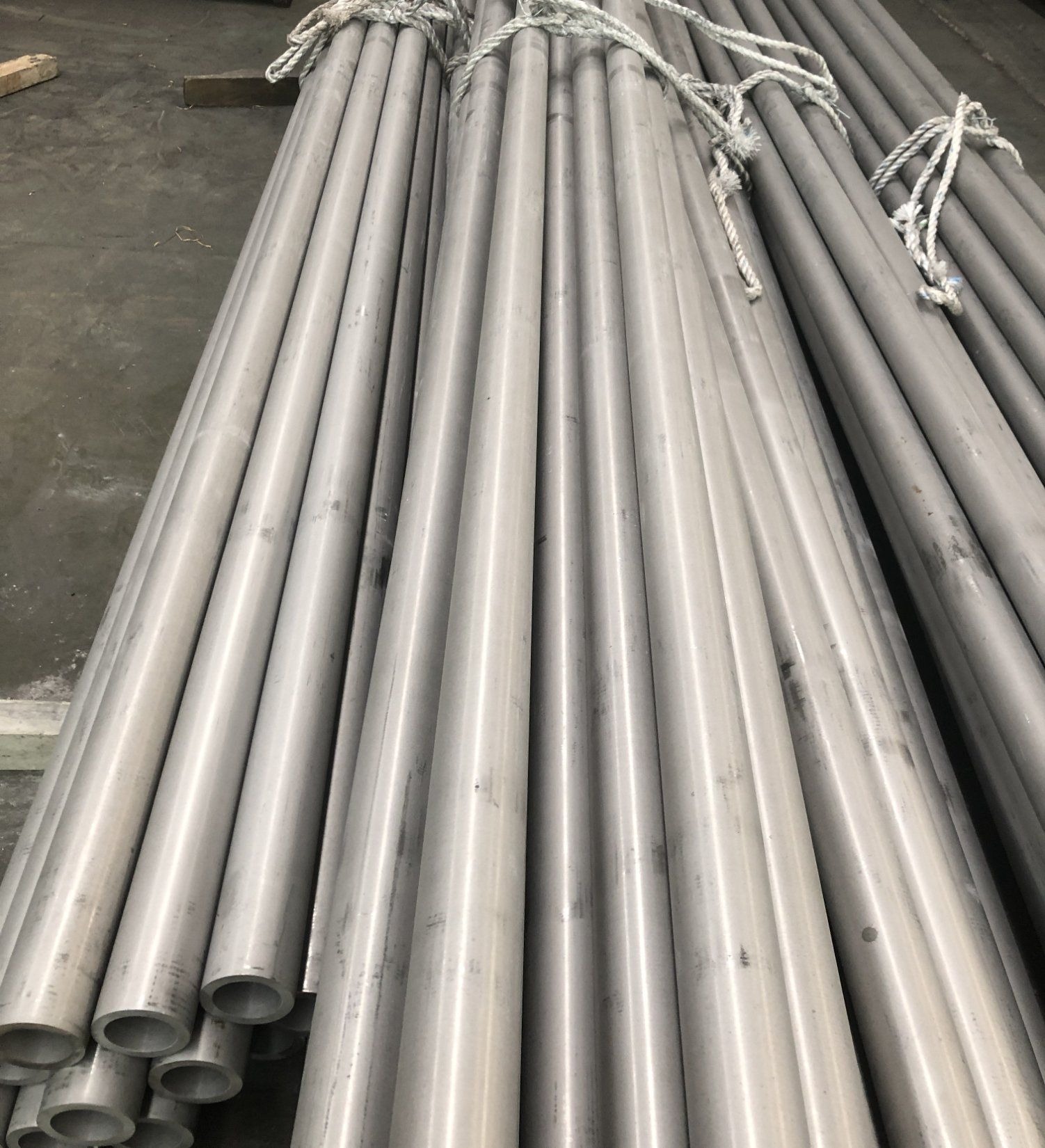
Inconel 625 Steel Pipe (UNS N06625 / W.Nr. 2.4856): Parameters, Specifications, Detailed Scientific Analysis
Introduction to Inconel 625
Inconel 625, designated as UNS N06625 or W.Nr. 2.4856, stands out as a premier nickel-based superalloy, celebrated for its remarkable strength, corrosion resistance, and adaptability in extreme conditions. This alloy, primarily composed of nickel (minimum 58%), chromium (20-23%), molybdenum (8-10%), and niobium (3.15-4.15%), is meticulously engineered for environments where high temperatures, corrosive media, and mechanical stresses converge. Trace elements such as titanium, aluminum, and iron further enhance its properties, making it a top choice for industries like aerospace, marine engineering, chemical processing, and nuclear energy. Inconel 625 pipes, available in seamless and welded forms, are vital for systems demanding durability in harsh settings. This article offers an in-depth exploration of Inconel 625 pipe specifications, including detailed parameters, comparative data, and recent scientific insights, crafted for engineers, researchers, and industry professionals seeking robust material solutions.
The alloy’s exceptional resistance to pitting, crevice corrosion, and chloride-induced stress corrosion cracking (SCC) makes it ideal for marine and chemical applications. Its high tensile strength, creep resistance, and oxidation resistance up to 1050°C ensure reliable performance in high-temperature environments like gas turbines and heat exchangers. Manufactured to standards such as ASTM B444, ASTM B704, and ASME SB-444, Inconel 625 pipes deliver consistent quality in seamless, welded, or clad configurations. This analysis covers the alloy’s chemical composition, mechanical properties, corrosion resistance, and applications, supported by detailed tables and comparisons with other alloys to underscore its strengths and limitations.
Chemical Composition
Grade | C | Mn | Si | P | S | Cr | Nb + Ta | Co | Mo | Fe | Al | Ti | Ni |
625 | ≤0.10 | ≤0.50 | ≤0.50 | ≤0.015 | ≤0.015 | 20.0 – 23.0 | 3.15 -4.15 | ≤1.0 | 8.0-10.0 | ≤5.0 | ≤0.40 | ≤0.40 | Bal |
Mechanical Properties
Material | Form and Condition | Tensile Strength MPa | Yield Strength (0.2% Offset) | Elongation 4D(%) | Hardness HB | ||
ksi | MPa | ksi | MPa | ||||
Alloy 625 Bar | Annealed | ≥120 | ≥827 | ≥60 | ≥414 | ≥30 | ≤ 287 HB |
Alloy 625 Sheet | Annealed | ≥120 | ≥827 | ≥60 | ≥414 | ≥30 | 145-240 |
Alloy 625 Tube3 | Annealed | ≥120 | ≥827 | ≥60 | ≥414 | ≥30 | – |
Alloy 625 Tube4 | Solution annealed | ≥100 | ≥690 | ≥40 | ≥276 |
Standard
Pipe Seamless | ASTM B444, ASTM B829, ASME SB 444, ASME SB 829, BS3074 NA21 |
Pipe Welded | ASTM B705, ASTM B775, ASME SB 705, ASME SB 775 |
Tube Seamless | ASTM B444, ASTM B829, ASME SB 444, ASME SB 829, AMS 5581, BS3074 NA21, AMS 5581 Type 1 |
Tube Welded | ASTM B704, ASTM B751, ASME SB 704, ASME SB 704, AMS 5581, AMS 5581 Type 2 |
Tube | VdTUV 499, ISO 6207, DIN 17751, ASME Code Case 1935 |
Fittings | ASTM B 366, ASME SB 366 |
Chemical Composition and Microstructure
The chemical composition of Inconel 625 forms the bedrock of its superior performance. With a minimum nickel content of 58%, the alloy establishes a stable austenitic matrix, resistant to chloride-ion SCC. Chromium (20-23%) bolsters oxidation resistance, while molybdenum (8-10%) and niobium (3.15-4.15%) provide solid-solution strengthening, eliminating the need for precipitation-hardening treatments. Trace elements like iron (≤5%), titanium (≤0.40%), and aluminum (≤0.40%) refine its properties, enhancing resistance to intergranular corrosion and high-temperature stability. The table below outlines the chemical composition:
Element | Composition (% by Weight) |
---|---|
Nickel (Ni) | ≥58.0 |
Chromium (Cr) | 20.0–23.0 |
Molybdenum (Mo) | 8.0–10.0 |
Niobium + Tantalum (Nb+Ta) | 3.15–4.15 |
Iron (Fe) | ≤5.0 |
Titanium (Ti) | ≤0.40 |
Aluminum (Al) | ≤0.40 |
Carbon (C) | ≤0.10 |
Manganese (Mn) | ≤0.50 |
Silicon (Si) | ≤0.50 |
Phosphorus (P) | ≤0.015 |
Sulfur (S) | ≤0.015 |
Cobalt (Co) | ≤1.0 (if determined) |
The microstructure of Inconel 625 is predominantly austenitic, featuring a face-centered cubic (FCC) crystal structure stabilized by niobium. This prevents sensitization during welding, reducing the risk of intergranular corrosion. The high molybdenum content enhances resistance to pitting and crevice corrosion in chloride-rich environments like seawater. However, prolonged exposure to temperatures between 550-700°C can trigger aging hardening, slightly reducing plasticity due to the formation of gamma double prime (γ″) phases. This requires careful consideration in applications with long-term high-temperature exposure. Compared to Inconel 718, which relies on precipitation hardening, Inconel 625’s solid-solution strengthening ensures consistent performance without complex heat treatments, simplifying fabrication and welding processes.
Mechanical Properties and Heat Treatment
Inconel 625 pipes exhibit outstanding mechanical properties across a broad temperature range, from cryogenic to 1093°C (2000°F). The alloy’s strength stems from the solid-solution hardening of its nickel-chromium matrix, enhanced by molybdenum and niobium. ASTM B444 defines two grades for Inconel 625 pipes: Grade 1 (annealed) and Grade 2 (solution-annealed). The mechanical properties vary by heat treatment, as shown below:
Property | Grade 1 (Annealed, ≥871°C) | Grade 2 (Solution-Annealed, ≥1093°C) |
---|---|---|
Tensile Strength (MPa) | ≥827 (120 ksi)</td | ≥690 (100 ksi) |
Yield Strength (MPa) | ≥414 (60 ksi) | ≥276 (40 ksi) |
Elongation (%) | ≥30 | ≥30 |
Hardness (HB) | 145–220 | 145–240 |
Grade 1, annealed at ≥871°C, provides higher tensile and yield strengths, making it suitable for applications requiring robust mechanical performance, such as aerospace components. Grade 2, solution-annealed at ≥1093°C, prioritizes corrosion resistance, ideal for chemical processing environments. The alloy’s ≥30% elongation ensures ductility, allowing it to withstand deformation without fracturing. Its creep resistance is notable, with minimal deformation under prolonged stress at high temperatures, making it perfect for boiler components and flare stacks. Compared to Incoloy 825, with a tensile strength of approximately 586 MPa, Inconel 625’s ≥827 MPa in Grade 1 offers superior strength. Incoloy 825, however, excels in sulfuric acid resistance due to its copper content (1.5-3%). Inconel 625’s weldability, without requiring post-weld heat treatment, enhances its appeal for pipe fabrication.
Corrosion Resistance and Environmental Performance
Inconel 625’s corrosion resistance is a defining feature, making it a top choice for pipes in aggressive environments. The alloy excels in resisting pitting, crevice corrosion, and chloride-induced SCC, particularly in seawater and sour gas wells. Its high nickel and molybdenum content ensures near-complete immunity to chloride SCC, a common issue in stainless steels. Tests in boiling 65% nitric acid show a corrosion rate of approximately 0.76 mm/year, while in stagnant seawater over three years, the maximum pit depth was only 0.025 mm, highlighting exceptional durability. The alloy also resists hydrochloric acid (HCl) across a wide range of concentrations at ambient temperatures, with minimal metal loss in high-temperature HCl tests.
In oxidizing environments, the chromium content provides robust protection up to 1050°C, though niobium can reduce oxidation resistance above this temperature. In reducing environments, the nickel-molybdenum combination ensures stability, making Inconel 625 suitable for chemical processing equipment exposed to acids like phosphoric and sulfuric. The alloy’s resistance to carburization is notable, with low carbon absorption (9.9 mg/cm²) in tests at 1090°C, ideal for hydrocarbon processing. However, in high-velocity combustion gas streams above 1050°C, Inconel 625 shows reduced oxidation resistance, losing 0.12-0.19 mm after 1000 hours at 980°C. Compared to Hastelloy C-276, with higher molybdenum (15-17%), Inconel 625 offers similar corrosion resistance but superior high-temperature strength due to niobium stabilization.
Manufacturing and Fabrication
Inconel 625 pipes are produced in seamless, welded, or clad forms, adhering to standards like ASTM B444 (seamless), ASTM B704 (welded), and ASTM B829 (general requirements). Seamless pipes, cold-drawn for precision, range from 4 mm to 219 mm in outer diameter, with wall thicknesses from 0.5 mm to 20 mm (schedules 5 to 160). Welded pipes, including ERW and EFW types, can reach up to 1219.2 mm in diameter, suitable for large-scale applications like offshore pipelines. Clad pipes, where Inconel 625 is bonded or weld-overlaid onto carbon steel, provide cost-effective corrosion resistance for oil and gas systems.
Welding Inconel 625 supports processes like GTAW (TIG), GMAW (MIG/MAG), and SMAW (MMA). The alloy’s niobium content prevents sensitization, eliminating post-weld heat treatment. Machining, however, requires low cutting speeds and sharp tools to avoid work-hardening. Forging is performed at 1010-1175°C, with uniform reductions to prevent duplex grain structures. Electropolishing enhances surface finish for corrosion resistance. Compared to Inconel 718, Inconel 625’s austenitic matrix simplifies fabrication, though its high shear strength demands rigid machine setups. The alloy’s compliance with standards like ASME B16.5 and ANSI B36.19 ensures industry compatibility.
Applications and Industry Use
Inconel 625 pipes are integral to industries requiring robust performance in extreme conditions. In aerospace, they are used in engine exhaust systems, thrust reversers, and ducting due to their high-temperature strength and fatigue resistance. The alloy’s ability to withstand thermal cycling from cryogenic to 1093°C makes it ideal for turbine components. In marine engineering, Inconel 625 pipes are employed in seawater heat exchangers, submarine components, and offshore platform flare stacks, leveraging their chloride SCC resistance. In the oil and gas sector, clad pipes are prevalent in sour gas wells, where hydrogen sulfide and sulfur at high temperatures pose corrosion risks.
Chemical processing benefits from Inconel 625’s compatibility with acids like nitric, phosphoric, and hydrochloric, used in scrubbers and reactors. Nuclear reactors utilize the alloy for its stability under radiation and high-temperature steam. Compared to Monel 400, which excels in reducing environments but lacks high-temperature strength, Inconel 625 offers broader applicability. Its use in waste-to-energy plants and biofuel production highlights its role in emerging technologies, though its higher cost necessitates careful cost-benefit analysis for large-scale projects.
Comparative Analysis with Other Alloys
Property/Alloy | Inconel 625 | Incoloy 825 | Hastelloy C-276 | 316L Stainless Steel |
---|---|---|---|---|
Nickel Content (%) | ≥58 | 38–46 | 57 | 10–14 |
Tensile Strength (MPa) | ≥827 | ≥586 | ≥790 | ≥515 |
Corrosion Resistance | Excellent (oxidizing/reducing) | Good (sulfuric acid) | Excellent (reducing acids) | Moderate (chloride SCC) |
Max Temperature (°C) | 1093 | 550 | 1040 | 800 |
Weldability | Excellent | Good | Good | Good |
Cost (Relative) | High | Moderate | High | Low |
Inconel 625 outperforms 316L in high-temperature and corrosive environments, making it a premium choice for critical applications. Incoloy 825 is cost-effective for less demanding conditions, while Hastelloy C-276 excels in specific reducing environments but is less versatile in oxidizing conditions. Inconel 625’s balanced properties make it a go-to material for pipes requiring reliability across diverse conditions.
Recent Scientific Insights and Developments
Recent studies underscore Inconel 625’s evolving role in advanced applications. Research from 2023 highlights its performance in additive manufacturing, where laser-welded pipes exhibit improved fatigue resistance compared to traditional welding. Thermal spray coatings, such as HVOF, enhance corrosion resistance in high-velocity gas streams, addressing limitations above 1050°C. The alloy’s low-cycle fatigue (LCF) variant, Alloy 625 LCF, shows promise in bellows and flexible piping. Testing in sour gas environments at 191°C revealed minor stress-corrosion cracking in cold-worked Inconel 625, suggesting careful heat treatment. Advances in weld overlay techniques have improved the cost-effectiveness of clad pipes, particularly in oil and gas applications.
Conclusion
Inconel 625 (UNS N06625 / W.Nr. 2.4856) is a cornerstone material for pipes in demanding environments, offering unmatched corrosion resistance, mechanical strength, and fabricability. Its high nickel, chromium, and molybdenum content, combined with niobium stabilization, ensures performance in aerospace, marine, chemical, and nuclear applications. While its cost is higher than alternatives like Incoloy 825 or 316L, its durability and versatility justify the investment. Ongoing research continues to expand its applications, particularly in additive manufacturing and advanced welding techniques, making Inconel 625 pipes a reliable solution for challenging industrial needs.
You must be logged in to post a comment.