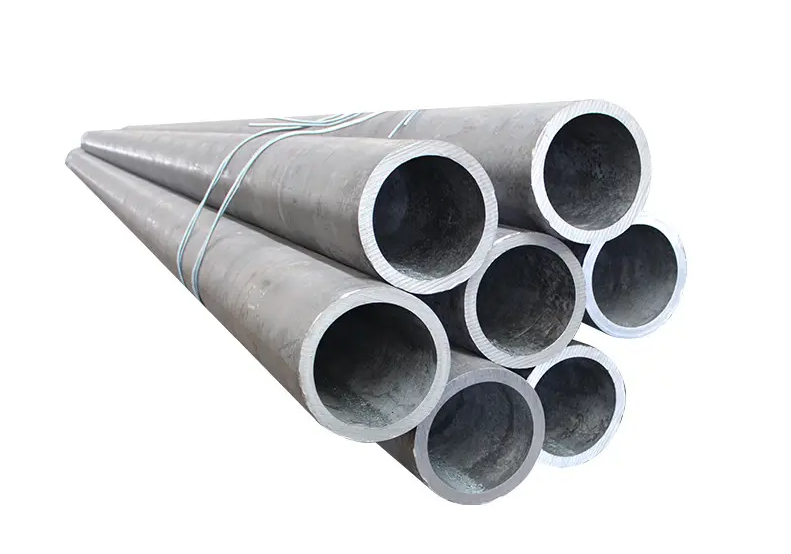
Kaedah untuk mengimpal saluran paip berdinding tebal tekanan tinggi keluli A335 P91 domestik: bidang teknikal – Ciptaan sekarang berkaitan dengan bidang teknologi kimpalan, khususnya yang berkaitan dengan kaedah untuk mengimpal saluran paip berdinding tebal tekanan tinggi keluli A335 P91 domestik.
Kami mempunyai inventori Terbesar ASTM A335 P91 Alloy Steel Seamless Pipe
Paip Keluli Aloi A 335 P91:
Saiz : 1/2″ untuk 24 “DAN DARI & NB
Jadual: SCH20, Sch30, SCH40.
Jenis : Golek / Direka / LANCAR
Panjang : Rawak Tunggal, Rawak Berganda & Panjang Potong.
akhir : Akhir Biasa, Hujung Serong.
Bahan-bahan :
Paip Keluli Aloi A335 P91 – Paip AS A335 P91
ASTM A335, Gr. P5, P9, P11, P12, P21, P22 & P91
ASTM A335 P91 Komposisi Paip Chrome
Gred | UNS | C≤ | MN | P ibu | S ibu | Si≤ | Cr | Mo |
P1 | K11522 | 0.10~0.20 | 0.30~0.80 | 0.025 | 0.025 | 0.10~0.50 | – | 0.44~0.65 |
P2 | K11547 | 0.10~0.20 | 0.30~0.61 | 0.025 | 0.025 | 0.10~0.30 | 0.50~0.81 | 0.44~0.65 |
P5 | K41545 | 0.15 | 0.30~0.60 | 0.025 | 0.025 | 0.50 | 4.00~6.00 | 0.44~0.65 |
P5b | K51545 | 0.15 | 0.30~0.60 | 0.025 | 0.025 | 1.00~2.00 | 4.00~6.00 | 0.44~0.65 |
P5c | K41245 | 0.12 | 0.30~0.60 | 0.025 | 0.025 | 0.50 | 4.00~6.00 | 0.44~0.65 |
P9 | S50400 | 0.15 | 0.30~0.60 | 0.025 | 0.025 | 0.50~1.00 | 8.00~10.00 | 0.44~0.65 |
P11 | K11597 | 0.05~0.15 | 0.30~0.61 | 0.025 | 0.025 | 0.50~1.00 | 1.00~1.50 | 0.44~0.65 |
P12 | K11562 | 0.05~0.15 | 0.30~0.60 | 0.025 | 0.025 | 0.50 | 0.80~1.25 | 0.44~0.65 |
P15 | K11578 | 0.05~0.15 | 0.30~0.60 | 0.025 | 0.025 | 1.15~1.65 | – | 0.44~0.65 |
P21 | K31545 | 0.05~0.15 | 0.30~0.60 | 0.025 | 0.025 | 0.50 | 2.65~3.35 | 0.80~1.60 |
P22 | K21590 | 0.05~0.15 | 0.30~0.60 | 0.025 | 0.025 | 0.50 | 1.90~2.60 | 0.87~1.13 |
P91 | K91560 | 0.08~0.12 | 0.30~0.60 | 0.020 | 0.010 | 0.20~0.50 | 8.00~9.50 | 0.85~1.05 |
P92 | K92460 | 0.07~0.13 | 0.30~0.60 | 0.020 | 0.010 | 0.50 | 8.50~9.50 | 0.30~0.60 |
Piawaian Komposisi Paip A335 Gr P91
Si, % | Cr, % | C, % | Mo, % | MN, % | P, % | N, % | S, % | V, % | Ni, % | NB, % | Al, % |
0.2 untuk 0.5 | 8.0 untuk 9.5 | 0.08 untuk 0.12 | 0.85 untuk 1.05 | 0.3 untuk 0.6 | 0.02 | 0.03 untuk 0.07 | 0.01 | 0.18 untuk 0.25 | 0.4 | 0.06 untuk 0.10 | 0.04 |
Jadual Kekuatan Mekanikal Paip ASTM A335 P91
memanjang | Sifat Tegangan | HB | Sifat Hasil |
20 | 585 | 250 | 415 |
Gred Bahan Setara Paip SA335 Gr P91
UNS | ASTM | Bersamaan Bahan | PERSATUAN JURUTERA MEKANIKAL AMERIKA |
---|---|---|---|
K91560 | A335 P91 | K90901, T91, 1.4903, X10CrMoVNb9-1 | SA335 P 91 |
ASTM | PERSATUAN JURUTERA MEKANIKAL AMERIKA | JIS G 3458 | UNS | BS | DARIPADA | ISO | ABS | NK | LRS |
---|---|---|---|---|---|---|---|---|---|
A335 P9 | SA335 P9 | STPA 26 | S50400 | 3604 P1 629-470 | 2604 II TS38 |
Latar belakang: Keluli A335 P91 ialah keluli 9Cr-1Mo yang diubah suai, terutamanya incorpo
A335P11 A335P91 A335P22 40cr 10CrMO910 35crmo 27SiMn Q345B 16Mn Paip Keluli Aloi Dikimpal
penarafan unsur aloi seperti V dan Nb ke dalam keluli tahan haba martensit 9Cr-1Mo asal. Keluli ini mempunyai rintangan pengoksidaan suhu tinggi yang sangat baik, rintangan kakisan wap suhu tinggi, dan rintangan rayapan, mengurangkan berat struktur dengan berkesan dan mencari aplikasi yang meluas dalam unit dandang yang besar, sistem saluran paip, dan industri petrokimia. bagaimanapun, disebabkan oleh sifat martensit yang disejukkan udara bagi keluli A335 P91, ia mempamerkan keplastikan yang lebih rendah dan kebolehkimpalan yang lebih lemah, mengenakan keperluan yang tinggi pada proses kimpalan, keliatan hentaman sambungan yang dikimpal, kerapuhan kimpalan, rawatan haba selepas kimpalan, dan zon kimpalan yang terjejas haba. Kimpalan keluli A335 P91 tradisional secara amnya menggunakan kimpalan arka tungsten gas manual (GTAW) untuk pas akar dan kimpalan arka logam terlindung manual (SMAW) untuk pengisian dan penutup, memerlukan kawalan ketat tenaga talian, panaskan suhu, dan suhu interpass semasa proses kimpalan. Kaedah ini memerlukan persekitaran kimpalan dan kemahiran pengimpal yang tinggi, dan kecekapan kimpalan manual adalah sangat rendah, memakan masa dan usaha, sangat menyekat kemajuan paip, menjejaskan jadual pembinaan, dan amat ketara untuk saluran paip berdinding tebal berdiameter besar.
Oleh itu, pemilihan rasional parameter dan proses kimpalan untuk keluli A335 P91 dan pembangunan keadaan proses kimpalan yang sesuai untuk pengeluaran memegang nilai praktikal dan ekonomi yang ketara.
Kandungan Reka Cipta: Untuk mengatasi kelemahan teknologi sedia ada, masalah teknikal yang perlu diselesaikan oleh ciptaan ini adalah untuk menyediakan kaedah untuk mengimpal saluran paip berdinding tebal tekanan tinggi keluli A335 P91 domestik, bertujuan untuk meningkatkan kecekapan kimpalan dan kimpalan kualiti, mengurangkan kos pembinaan dan keamatan buruh, dan menambah baik persekitaran kerja.
Bagi mencapai objektif di atas, ciptaan sekarang menggunakan penyelesaian teknikal berikut:
Kaedah untuk mengimpal saluran paip berdinding tebal tekanan tinggi keluli A335 P91 domestik, yang terdiri daripada langkah-langkah berikut mengikut urutan:
(1) Pemprosesan serong pra-kimpalan: Proseskan kawasan kimpalan saluran paip untuk dikimpal menjadi serong berbentuk V berganda, lakukan pemeriksaan penembus pewarna pada permukaan serong untuk memastikan tiada permukaan retak, dan bersihkan serong dan karat permukaan, minyak, dan oksida dalam kawasan 20mm pada kedua-dua belah serong;
Meneruskan kaedah kimpalan untuk paip keluli berdinding tebal A335 P91 yang dihasilkan di dalam negara:
- rawatan haba selepas kimpalan: Selepas mengimpal, tutup kedua-dua hujung paip dan gunakan pemanas elektrik untuk memanaskan kawasan pada kedua-dua belah kimpalan, sekurang-kurangnya 3 kali lebar kimpalan dan tidak kurang daripada 25mm. Panaskan kawasan itu pada julat suhu 750-770°C dan tahankannya 2.5-4 jam, bergantung pada ketebalan paip.
Sila ambil perhatian bahawa suhu dalam kaedah ini dipantau menggunakan termometer inframerah. Kaedah kimpalan untuk paip keluli berdinding tebal A335 P91 tekanan tinggi ini mempunyai kelebihan berikut:
-
Penggunaan pelbagai lapisan, kimpalan berbilang laluan mengurangkan luas keratan rentas setiap lapisan kimpalan, meningkatkan keliatan sambungan yang dikimpal dan mengelakkan penyempitan zon yang terjejas oleh haba dalam kimpalan tebal, serta pelembutan sambungan kimpalan semasa operasi jangka panjang pada suhu tinggi.
-
Kimpalan arka tungsten gas manual (GTAW) untuk kimpalan akar mempunyai kelajuan kimpalan yang lebih perlahan, dan pengedap kedua-dua hujung paip membantu mengawal suhu interlayer. Kimpalan arka tenggelam automatik (MELIHAT) untuk mengisi dan menutup lapisan mempunyai kelajuan kimpalan yang lebih cepat dan arus yang lebih tinggi, membebaskan haba dengan lebih cepat. Sekurang-kurangnya satu hujung paip hendaklah dibuka, dan kimpalan berterusan boleh dilakukan tanpa memerlukan kawalan suhu interlayer.
-
Menggunakan wayar kimpalan berdiameter kecil (tidak lebih daripada 2.5mm) dan fluks hidrogen rendah untuk kimpalan boleh mengurangkan tenaga linear semasa proses kimpalan, meningkatkan kadar pemendapan kimpalan, menapis butiran bahan asas, dan mengurangkan kemungkinan kecacatan seperti keliangan dan keretakan pada kimpalan.
-
Dalam persekitaran berangin, kesan perlindungan kimpalan arka tenggelam automatik adalah lebih baik daripada proses kimpalan arka lain.
-
Berbanding dengan kaedah kimpalan manual tradisional, kaedah ini berkesan memendekkan rawatan haba dan kitaran kimpalan, improves weld kualiti and welding efficiency, reduces labor intensity, and saves construction costs.
Implementation example 1: Using domestic A335P91 pipeline DN350 as the base material, the following welding method is adopted:
(1) The welding area of the pipe to be welded is processed into a double V-shaped groove as shown in Figure 1, with a blunt edge height of 1mm, a bottom angle of 60±5° in the direction of the pipe length, a height of 15mm, and an upper angle of 78-82° in the direction of the pipe length. The groove surface is colored inspected to ensure that there are no surface cracks on the groove. The surface rust, oil stains, oxides, dan lain-lain. within 20mm on both sides of the groove are cleaned;
(2) The two sections of the welded pipe are assembled, ensuring that the end face gap of the butt joint is 3-6mm, ketinggian adalah sekata, dan penjajaran tidak lebih daripada 1mm;
(3) Kimpalan arka argon manual GTAW digunakan untuk kimpalan bawah. Sebelum mengimpal, port hujung paip yang hendak dikimpal disekat, dan dinding dalam atau belakang kimpalan diisi dengan gas argon untuk perlindungan. Paip keluli yang akan dikimpal dipanaskan terlebih dahulu, dan suhu alur dipantau dalam masa nyata menggunakan termometer inframerah. Apabila suhu mencapai 160 ℃, kimpalan bermula, menggunakan dawai kimpalan ER90S-B9 dengan diameter untuk mengimpal tiga lapisan. Parameter proses dipilih seperti berikut: Sambungan positif DC bekalan kuasa, arus kimpalan 118A, voltan arka 14V, dan kelajuan kimpalan 3-10cm/min. Perhatian harus diberikan kepada perkara berikut semasa kimpalan arka argon manual GTAW: A) The surface of the workpiece to be welded should not be ignited by the arc, tested for current, or temporarily welded to support or clamp;b) The manual argon arc welding starts from the lowest point of the pipe to be welded, and is symmetrically welded by two people, with the welding joints staggered between 100-150mm; C) During manual argon arc welding, the preheating temperature on both sides of the groove should be monitored in real-time, and the preheating temperature should be strictly controlled between 150℃ and 200℃; D) During manual argon arc welding, wind protection measures should be taken, and the wind speed in the welding environment should not exceed 2m/s. There should be no draft in the pipe to be welded, and moisture, rain, and snow protection measures should be taken;
(4) Automatic submerged arc welding SAW is used for filling and covering. Before automatic submerged arc welding filling and covering, at least one end of the pipe to be welded is unblocked, and the welding area is preheated. When the temperature reaches 200℃, continuous welding begins, using EB9 welding wire with a diameter of and MARATHON543 welding flux for multi-layer and multi-pass filling and covering welding. The SAW welding parameters are selected as follows: DC reverse connection of the power supply, welding current of 280A, arc voltage of 28V, and welding speed of 25-45cm/min.
Attention should be paid to the following points during automatic submerged arc welding SAW:
A) The welding wire should be kept clean and dry, and the welding flux should be stored in a dry place to prevent moisture absorption;
b) The welding wire should be fed smoothly and evenly, and the welding flux should be added in time to ensure the welding kualiti;
C) The welding speed should be stable, and the welding gun should be kept perpendicular to the pipe axis to ensure the consistency of the weld bead;
D) The welding slag should be removed in time after each layer of welding is completed, and the surface of the weld should be cleaned with a wire brush or grinding wheel to ensure the quality of the next layer of welding;
e) The welding process should be monitored in real-time, and the welding parameters should be adjusted in time according to the actual situation to ensure the welding quality. After the welding is completed, the weld surface should be inspected visually and by non-destructive testing to ensure that there are no defects such as cracks, pores, Kemasukan Slag, and incomplete penetration. Akhirnya, the welded joint should be heat-treated according to the process requirements to eliminate welding stress and improve the mechanical properties of the welded joint.
Implementation example 2: Using imported A335P91 pipeline DN500 as the base material, the following welding method is adopted:
(1) The welding area of the pipe to be welded is processed into a double V-shaped groove as shown in Figure 1, with a blunt edge height of 1.5mm, a bottom angle of 60±5° in the direction of the pipe length, a height of 20mm, and an upper angle of 78-82° in the direction of the pipe length. The groove surface is colored inspected to ensure that there are no surface cracks on the groove. The surface rust, oil stains, oxides, dan lain-lain. within 20mm on both sides of the groove are cleaned;
(2) The two sections of the welded pipe are assembled, ensuring that the end face gap of the butt joint is 4-8mm, ketinggian adalah sekata, and the misalignment is not greater than 1.5mm;
(3) Automatic submerged arc welding SAW is used for bottom welding. Sebelum mengimpal, port hujung paip yang hendak dikimpal disekat, dan dinding dalam atau belakang kimpalan diisi dengan gas argon untuk perlindungan. Paip keluli yang akan dikimpal dipanaskan terlebih dahulu, dan suhu alur dipantau dalam masa nyata menggunakan termometer inframerah. When the temperature reaches 200℃, kimpalan bermula, using EB9 welding wire with a diameter of and MARATHON543 welding flux for multi-layer and multi-pass filling and covering welding. The SAW welding parameters are selected as follows: DC reverse connection of the power supply, welding current of 350A, arc voltage of 32V, and welding speed of 25-45cm/min. Attention should be paid to the following points during automatic submerged arc welding SAW: A) The welding wire should be kept clean and dry, and the welding flux should be stored in a dry place to prevent moisture absorption; b) The welding wire should be fed smoothly and evenly, and the welding flux should be added in time to ensure the welding quality; C) The welding speed should be stable, and the welding gun should be kept perpendicular to the pipe axis to ensure the consistency of the weld bead; D) The welding slag should be removed in time after each layer of welding is completed, and the surface of the weld should be cleaned with a wire brush or grinding wheel to ensure the quality of the next layer of welding; e) The welding process should be monitored in real-time, and the welding parameters should be adjusted in time according to the actual situation to ensure the welding quality.
(4) Automatic submerged arc welding SAW is used for filling and covering. Before automatic submerged arc welding filling and covering, at least one end of the pipe to be welded is unblocked, and the welding area is preheated. When the temperature reaches 250℃, continuous welding begins, using EB9 welding wire with a diameter of and MARATHON543 welding flux for multi-layer and multi-pass filling and covering welding. The SAW welding parameters are selected as follows: DC reverse connection of the power supply, welding current of 450A, arc voltage of 36V, and welding speed of 25-45cm/min. After the welding is completed, the weld surface should be inspected visually and by non-destructive testing to ensure that there are no defects such as cracks, pores, Kemasukan Slag, and incomplete penetration. Akhirnya, the welded joint should be heat-treated according to the process requirements to eliminate welding stress and improve the mechanical properties of the welded joint.
anda mesti log masuk untuk menghantar komen.